At the outbreak of the Second World War, the Australian government decided to build a blast furnace and shipyard near the then main source of iron ore at Whyalla in South Australia. However, as this site was on the edge of a desert, fresh water needed to be piped 360 km from Morgan on the Murray River. An above-ground welded steel pipe was proposed and the local Water Authority, responsible for the project, considered possible coatings. After investigation of possibilities available at that time, they decided that “nothing could hold a candle” to the newly developed inorganic zinc (IOZ) silicate. At this time, most steel was protected with oil-based coatings, which needed re-application every few years. Their faith was vindicated as the original coating is still largely intact over 70 years later. In fact, IOZ silicate either alone or part of a coating system, now probably protects more steel from the ravages of corrosion than any other single protective coating apart from galvanizing.
IOZ was developed by an Australian inventor working in his shed in suburban Melbourne. Victor Nightingall (1881-1947) had many interests, including agriculture, electric heating, and x-rays, and had taken out a number of patents. In the 1930s, he decided to try to develop a totally new type of protective coating by reacting sodium silicate (like a liquid glass) with zinc powder and applying it to a steel surface. He was hoping that the components would react together to form an iron-zinc-silicate mineral rather like a mixture of the minerals Williamite and Franklinite. We know now that the extent of reaction was restricted to the surface of the iron and zinc particles, but after much experimentation, he came up with a successful coating that clearly provided superior protection than any other product on the market. He coined the term “dimetallization” to describe the reaction between the zinc and iron, and formed the Dimet Co. to market the product. The coating required heating to cure it to sufficient hardness, but it was used successfully on a small number of projects in Melbourne before being adopted for the Morgan-Whyalla pipeline. After the war, it was adopted for other similar pipeline projects around Australia and became widely used for other applications where the stoving process was not an issue.
In 1949, Charles “Chuck” Munger of the Ameron Co. visited Australia to inspect the Morgan-Whyalla coating, and other similar projects. He was impressed and licensed the product for use in the United States, where it was marketed as Dimetcote† . The stoving process was, of course, a severe limitation and work by Ameron and in Australia developed a post-cured product where a curing agent was washed onto the coating after application. By the 1960s, self-curing waterborne products were available, soon followed by solventborne products, simplifying application even further. These are the products in use today and are marketed by most large paint companies around the world.
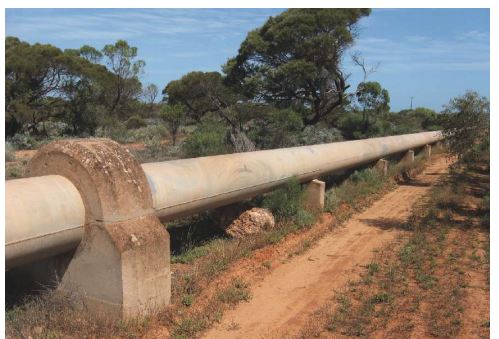
IOZ silicates are remarkable coatings and unlike other paints in many ways. Being inorganic, they are unaffected by sunlight, ultraviolet radiation, rain, dew, bacteria, fungi, or temperatures up to ~400 °C. If they are damaged or worn away, the zinc continues to provide galvanic protection to the underlying steel and porosity in the coating is filled with corrosion products. As the zinc is further consumed, rust may start forming but will not grow under the intact zinc coating, unlike normal paints. They resist most organic solvents and have excellent friction characteristics. In fact, they are usually the only coating allowed when structures contain friction-grip joints. Most importantly, a properly applied single coat of IOZ will give excellent protection to steel for years or indeed decades, even in some quite aggressive environments. They are truly unique and it is little wonder that they have revolutionized the means of protecting steel structures from corrosion.
However, their importance goes beyond the coating and corrosion industry. Chuck Munger’s view,1 while perhaps a little over the top, is worth quoting as a final tribute to Victor Nightingall, and the product he invented: “Inorganic zinc coatings have been one of the true technological developments of our time which has made a real and positive impact on modern society. While this impact is not as dramatic as that of television or space travel, inorganic zinc coatings have nevertheless made a solid contribution toward the preservation of scarce materials, thus eliminating the need for replacement of existing structures, reducing the cost of steel structures, saving manpower, reducing the energy required for metal replacement, and providing new structures with a substantial increase in life expectancy.”
Further reading: R.A. Francis (ed.), Inorganic Zinc Coatings: History, Chemistry, Properties, Applications and Alternatives, Australasian Corrosion Association ebook (2013).
Reference
1 C.G. Munger, Corrosion Protection by Protective Coatings, 2nd ed. (Houston, TX: NACE International, 1999), p. 133.
C.G. Munger, Corrosion Protection by Protective Coatings, 2nd ed. (Houston, TX: NACE International, 1999), p. 133.