In about 88 AD, a remote Roman legion at the Inchtuthil fortress on the north bank of the Tay River was ordered back to the European mainland. Unable or unwilling to transport nearly a million iron nails with it, the legion dug a pit and buried them. Since iron could be used for weapons, agriculture, and buildings in those days, it was highly prized by the enemy of the Roman legions.
It was nearly 1,900 years before the nails were found. In 1961, archaeologist Sir Ian Richmond noticed a region of different colored earth at the Inchtuthil site. After digging for several meters, he came across a large corroded mass of iron consisting of nearly 10 tonnes of nails and other small iron implements. Further investigation found that the outer items were badly corroded with a solid crust of iron oxide; however, those on the inside had only a minimal amount of rust on the surface.
The survival of the central nails was attributed to protection from corrosive water and oxygen by the outer solid crust, which had formed a protective barrier. It is not possible to know how much water or oxygen the inner nails were exposed to over the centuries, but clearly the amount was very small or the exposure time was very short. Information on water, soil composition, and other chemical factors at the site was not obtained. But the survival of iron on a river flood plain for nearly two millennia does present further evidence that protecting iron from water or oxygen exposure, or both, can prevent or at least minimize corrosion damage.
Many of the nails were sent to museums, corrosion associations, and other interested persons around the world as gifts. These nails, in various sizes, were mounted in a wooden box with a clear plastic lid and a white plastic label. A box containing five square shank section nails with flat, circular heads was sent to the 1943 – 2018 NACE International 75 Roman iron nails from Inchtuthil were presented to the Australasian Corrosion Association in the 1960’s. The larger nails have suffered subsequent rusting, probably from corrosive fumes emitted by the wooden case. Australasian Corrosion Association. The nails, with approximate lengths of 195, 170, 135, 90, and 50 mm, are now in rather poor condition with dark flaking rust, especially on the larger nails.
Similar boxes occasionally appear in auctions and on web sites, and most of these nails also appear to be severely corroded. It may be that exposure to humidity over the past 50 years has caused the small amount of original rust on them to grow; however, it is more likely that acetic acid (CH3COOH) fumes from the wooden box were the main contributor to the additional corrosion. The corrosion products, which show black magnetite typical of rust formed in severe environments, would support this hypothesis.
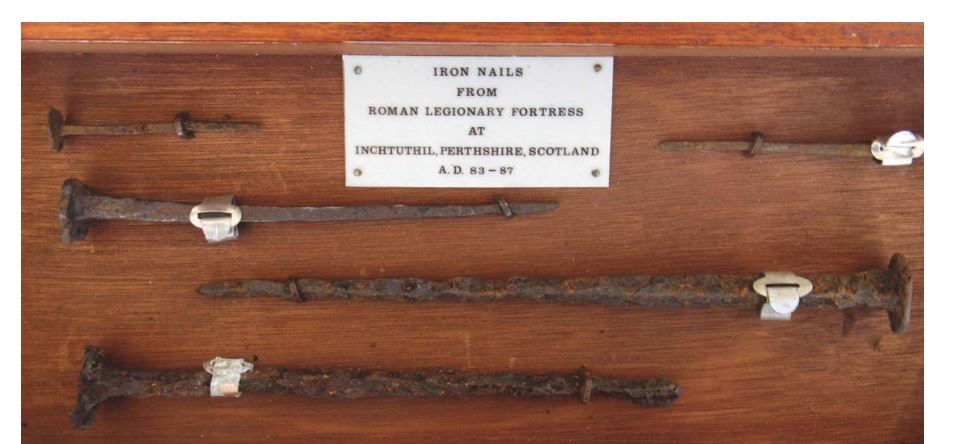
Metallurgical investigations of the nails have been carried out since their discovery and show the microstructure and properties typical of ancient wrought iron objects. Iron could not be obtained as a liquid from iron ore at temperatures and technology available to the ancients. Around 1300 BC, however, the Hittites (who lived in what is now eastern Turkey) are believed to have discovered that heating iron ore to ~1,200 °C in a charcoal-fuelled furnace reduces the iron oxide to iron metal, and hammering enables the impurities to be driven out as slag. The result was a strong and tough metal that consisted of a mixture of almost pure iron with the remaining slag forming longitudinal inclusions (known as stringers) spread throughout the metal. In regions where the metal contacted the charcoal in the furnace, a higher carbon content was achieved. During the subsequent centuries, this technology spread west across the ancient world to Europe.
The first stage of producing iron objects usually involved semi-finished slabs of iron, known as blooms, that were produced by repeatedly heating, hammering, and folding the mass of metal. In a second separate process by the local blacksmith, the blooms were forged into finished products such as weapons, ploughshares, nails, etc. Ancient iron usually possesses a heterogeneous microstructure of mainly low-carbon areas with some high-carbon areas and slag stringers, which gives it highly variable mechanical properties such as hardness.
The Inchtuthil nails are no exception, and have a range of high- and low-carbon micro-structures. The larger nails tend to have a higher proportion of high-carbon regions than the smaller nails, which indicates the Roman smiths may have known of the need for higher strength in larger items. Although the corrosion of ancient iron shows no relationship to the micro-structure, the Roman nails show us that it is possible to protect a metal from corrosion by minimising exposure to moisture.