Austenitic stainless steels (SSs) have been used as structural materials for various components in the aqueous reprocessing plants. These alloys are widely used in nuclear spent fuel reprocessing and waste management plants and the process fluid is nitric acid at temperature up to boiling point. Incorporation of oxidizing ions in nitric acid stream make the environment highly corrosive to stainless steels. Several types of nitric acid grade (NAG) alloys having compositions similar to Types 304L, 310L, and several new proprietary alloys have been developed worldwide. NAG alloys show lower corrosion rates compared to conventional Type 304L in boiling HNO3 (Huey). However, several reports of failure have been reported in components made of NAG grade austenitic SS also. In this study it has been shown that the potential attained in process solution determines the corrosion behaviour of SS. Potentials were applied to Types 304 L NAG, and 310L in boiling 6 M nitric acid for a period of 48 h and corrosion behaviour was observed. Influence of Cr6+ concentration present in nitric acid solution on end grain corrosion rate was also studied. Some important observations of this investigation were: (1) Rate of IGC increased exponentially with the increase in the applied potential. (2) No significant difference in corrosion rate of Type 304L NAG1 having step and dual microstructures was observed (3) Increase in Cr6+ concentration present in nitric acid solution increase end grain corrosion rate of Type 304L NAG2.
Presenter
Muhammad Hussain
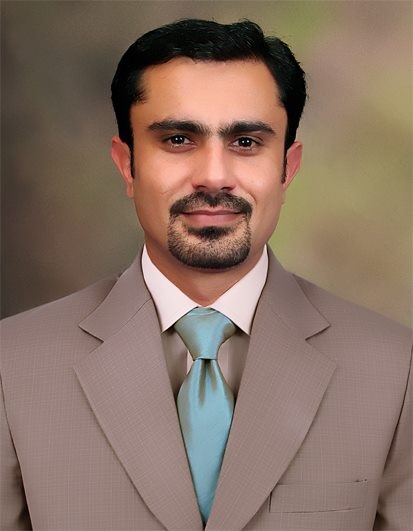
Muhammad Hussain has over 10 years’ experience in improving business outcomes by driving up plant performance while reducing cost and risk through managing asset reliability. Muhammad is an accredited professional and chartered engineer by Engineers Australia in Materials Engineering and Asset Management. Muhammad is Fellow of Institute of Materials, Minerals & Mining (IOM3) and Institute of Corrosion (ICorr) in the UK.