If you work in corrosion control, you will undoubtedly come across epoxy coatings. They are used wherever steel has to be protected against corrosion— offshore platforms, onshore oil and gas production, refineries, petrochemical plants, power plants, bridges, ships, wharfs, and many more. They will protect steel in the atmosphere from rusting by preventing oxygen and water from reaching the surface. They will prevent the interior of steel tanks from reacting with cold water, hot water, petroleum, and other organic products and many other acidic, alkaline, and pH neutral chemicals. For good measure, they are also used to protect other surfaces such as concrete and nonferrous metals. If you had to name the most versatile method of preventing corrosion, an epoxy coating would be a good choice.
So what is it that makes epoxy such a useful chemical? The term epoxy refers to thermosetting polymers (one that cures irreversibly by molecules cross-linking) produced by the reaction of an epoxide group (often also confusingly called an epoxy group), which is a three-membered ring of an oxygen atom attached to two adjacent carbon atoms. The ring structure of the epoxide group is easily opened and provides a site for crosslinking to form the final polymer. The epoxide group is on a small molecule, most commonly epichlorohydrin (ECH), which is reacted with a much larger molecule containing lots of carbon ring (aromatic) and chain (aliphatic) structures, most commonly bisphenol-A (BPA) to form what is known as an “epoxy prepolymer.” This is a large polymer molecule, but still a liquid, and forms the resin half of the final product. It needs to react with a hardener (also called a converter) to cure to form the final, highly crosslinked product that is strong, hard, and provides the required corrosion resistance. No volatiles are given off during cure so shrinkage is much less than for other polymers. One common hardener is polyamine, or simply amine, which is an organic molecule containing nitrogen and hydrogen atoms rather like ammonia. The hydrogen atoms on the amine react with the oxygen atoms on the epoxy prepolymer to form the three-dimensional cross-linked polymer that gives the final product its excellent properties. The polymer has many charged molecular groups such as hydroxides, which make it polar and ensure good adhesion to metallic surfaces. Furthermore, the carbon-carbon and other linkages along the polymer chain are strong and very stable, giving epoxies their good chemical resistance, strength, and toughness. At the same time, cross-linking is just sufficient enough to give the film some flexibility
There are a range of epoxy types depending on the resin or hardener used, making epoxies one of the most versatile polymers. Other resins than BPA include bisphenol F and novalac, which have improved resistance to certain chemicals. As well as amine, another common hardener is polyamide, which has lower shrinkage on curing, increases the flexibility of the film, and gives a longer pot life, but has reduced chemical resistance. For atmospheric coating systems, a polyamide hardener is generally used, and there are pigmented and nonpigmented primers and intermediate coats. The major weakness of epoxies exposed to the atmosphere is that they chalk due to reaction with ultraviolet light, so they are not used as topcoats where color or gloss are important, although chalking has only a minor effect on durability. For maintenance work where abrasive blasting is often not possible, surface-tolerant epoxies (or epoxy mastics) that are formulated to soak into poorly prepared surfaces as well as dry slowly are the usual primer of choice. For more aggressive environments such as splash zones, very high-build or ultrahigh-build epoxies are often specified. For tank linings, solventless epoxies with or without glass reinforcement are ideal. For pipelines, powder coatings (fusion-bonded epoxies) are used alone or as part of a three-layer system. Various additives and modifications can create products for high temperatures, wear and abrasion resistance, fire resistance, and non-slip flooring.
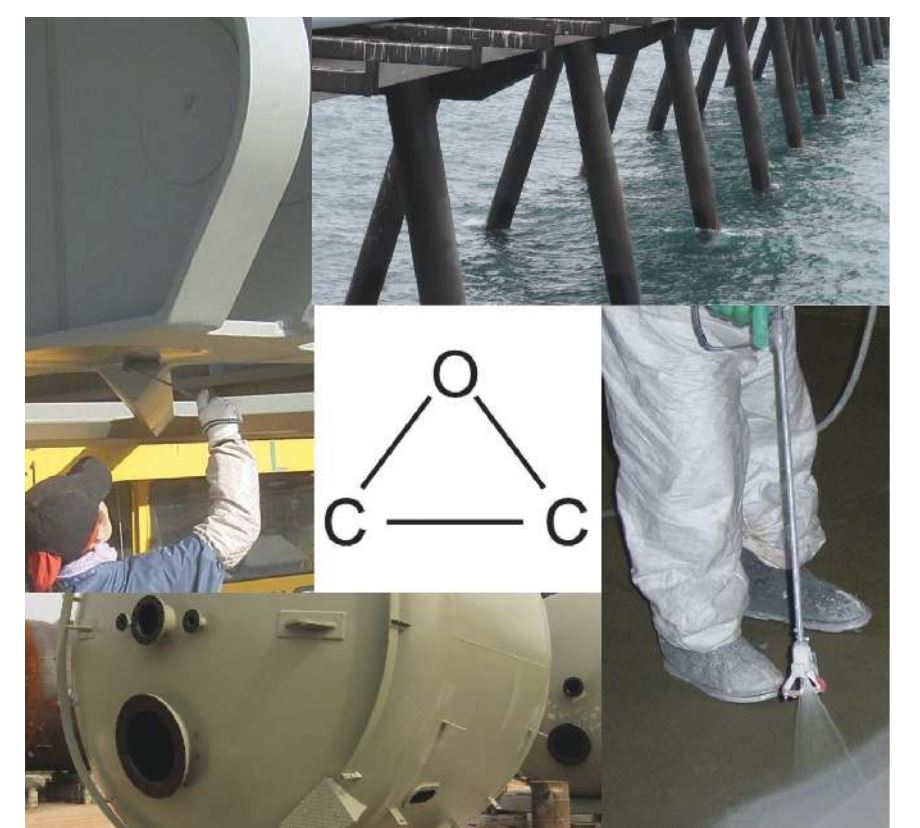
The first true commercial bisphenol epoxy resins were discovered in the late 1930s by Pierre Castan working in Switzerland for the company that eventually became Ciba-Geigy. He was attempting to find a product that could be used for dentures, but this was not commercially successful. At around the same time, Sylvan Greelee, working for the Devoe-Raynolds in the USA, was reacting bisphenol-A with fatty acids to produce an air-drying coating. Various chemical companies developed this original research after World War II and commercial epoxy resins for coatings made their debut in the late 1940s. Protective coatings were one of the first and are still the most important application of epoxies, accounting for around 50% of all epoxy resins produced, but epoxies are also found in adhesives, castings, flooring, and many other uses.
Unlike inorganic zinc silicate with the Morgan-Whyalla pipeline, there is no classic icon from the early days that shows the durability that can be achieved with epoxy coatings. Near the tomb of Sir Christopher Wren in his masterpiece, St Paul’s Cathedral in London, is the inscription, “If you seek his monument, look around you.” If you are in the corrosion control industry, look around you. You will undoubtedly see examples of this remarkable and valuable means of corrosion protection.