R.E. Melchers
Centre for Infrastructure Performance and Reliability,
The University of Newcastle, Australia
SUMMARY: Management of reinforced concrete assets increasingly relies on analytical models to predict the time to reinforcement corrosion, particularly to serious, damaging corrosion. Increasingly it is found that predictions by existing models for the onset of chloride-induced reinforcement corrosion do not compare well with observations and practical experience for actual concrete structures. Examples are given to show that for high quality concrete structures very high levels of chlorides can exist without signs or evidence of corrosion, even after long-term exposures. In this context, recent research that separates corrosion initiation from active corrosion is reviewed. Corrosion initiation is dominated by presence of air voids adjacent to the reinforcement. It is mainly a short-term transient effect that does not signal the commencement of serious corrosion. Active corrosion is the direct result of reduction of concrete alkalinity, a mechanism accelerated by chlorides. This, rather than direct chloride attack, is the cause of serious reinforcement corrosion. Also, the role of stress-induced and other concrete cracking must be reconsidered. These new interpretations open up the way for improved modelling and prediction of ‘chloride-induced’ corrosion.
Keywords: Corrosion, Reinforcement, Alkalinity, Structures, Pitting, Quality.
- INTRODUCTION
Increasingly asset managers and engineers are interested in the durability of reinforced concrete (RC) assets, and in particular durability against reinforcement corrosion. Much of structural and infrastructure engineering is about prediction – the probability of a structure remaining safe over a proposed lifetime, or the estimated lifetime for a given probability of failure. Such prediction is based on analytical (mathematical) models, calibrated to field experience and observations. This applies to the various types of loads that may be applied to a structure. It also applies for the resistances or load capacities of various types of materials and structural systems. Clearly, if deterioration is to be included in such analyses, models for prediction of the likely level of deterioration at the structural engineering level are required, ideally to a corresponding level of sophistication and calibrated to reality and relevant past experience. Prediction of expected behaviour of structures and their deterioration is important because (1) there are many reinforced concrete structures still in existence in practice and (2) there are economic and environmental benefits in producing reinforced concrete structures with long-term durability.
Models used for prediction can be at various levels of sophistication and at various levels of detail. In all cases they must be based on a sound understanding of the fundamental processes involved although this can depend on the level of abstraction that is appropriate for the intended use. For example, designers of, say, a Sydney Harbour bridge, do not need to know much about the atomic structure of steels but they do need to know how such steels behave at a level suitable for engineering design. This means that, irrespective of the level of abstraction, all models should be consistent with sound and coherent data. They also should be calibrated to such data. Ideally, models should be analytical so as to allow robust, valid and defendable extrapolation. In principle these requirements apply also to so-called ‘heuristic’ models and to knowledge within so-called ‘expert systems’. As soon as these are used for prediction there are assumptions about trends and about the validity and methodology for extrapolation, whether these are explicit or not. In all cases, prediction implies a model for extrapolation from the existing knowledge base. If that model is not understood or is poor, any prediction will be problematic at best and ‘hocus-pocus’ at worst.
In terms of deterioration of reinforced concrete (RC) structures, probably of most concern are structures exposed to marine environments, or to chloride conditions. The concrete matrix itself is seldom a significant factor, at least for many structures but could be for infrastructure such as sewer pipes (Wells and Melchers 2015). Herein, the durability of the concrete matrix itself is not considered. Also, by restricting attention mainly to high quality, low permeability concretes, carbonation of the concrete as a mechanism for reinforcement corrosion can be ignored. Practical experience has shown that for these, carbonation depths are only a few millimetres, even over extended periods of exposure (Parrott 1987). Similarly, issues such as alkali aggregate reactions are ignored herein.
Marine environments are perceived as causing aggressive corrosion, and hence structural damage, relatively quickly, particularly for structures not protected from the environment. There are many examples in practice to support this perception (e.g. Wig & Ferguson, 1917; Wakeman et al.1958; Lewis & Copenhagen, 1959; Lewis, 1962; Gjorv, 1971, 1994). Protection can be in the form of physical barriers such as ceramic or other low permeability tiles, protective coatings such a durable paints, bituminous materials or thick membranes, waterproofed concrete cover or enclosure within the weatherproof skin of a building. It also can be in the form of cathodic prevention for new structures or cathodic protection for structures already showing signs of distress. When these systems are used, and provided they are well-designed, well executed and, importantly, well-maintained, long-term durability is unlikely to be an issue. Alternative systems, that avoid the use of steel reinforcement, usually lack the strength, ductility, or economy normally associated with conventional steel reinforced concretes. However, the question must be asked whether these protection or alternative systems are strictly necessary.
It is sometimes forgotten that there is a considerable documented history of successful, durable reinforced concrete structures, exposed, unprotected, to marine environments for long periods of time (Wakeman et al. 1958; Lukas, 1985; Ozaki & Sugata 1998; Broomfield, 1999; Gjorv, 2009; Melchers et al. 2009; Angst et al. 2012; Melchers et al. 2017). There is evidence also that apparently very durable concrete structures have, historically, been made with seawater (and in some cases also with alkaline materials such as coral) (Wig & Ferguson, 1917; Narver, 1954; Wakeman et al. 1958; Dewar, 1963; Mather, 1964; Boqi et al. 1983; Burnside & Pomerening, 1984). Despite this experience, the use of seawater in concretes was banned in most countries during the 1960s, apparently (Richardson 2002; Gjorv, 2009) as a result of laboratory observations on reinforced concrete samples (Shalon & Raphael, 1959) and also based on some electrochemical tests (cf. Escalante and Ito, 1990).
It should be clear from this brief introduction that the building of models for the prediction of likely reinforcement corrosion in marine environments raises some interesting issues. There is much practical experience, that is, anecdotal ‘evidence’, but the mechanisms involved in the corrosion of reinforcement in concrete structures exposed to marine environments usually are considered still not fully understood, despite many decades of research. For this reason, reinforcement corrosion in marine environments currently is referred to as ‘chloride-induced’ corrosion. To help set this in context, the next section gives an overview of the current conventional wisdom for the theoretical, conventional, approach to predicting chloride-induced corrosion of reinforcement bars. A brief summary is then given of field experiences extracted from actual structures. This is followed by a description of some recent research results and an outline given of a more logical model. These developments throw new light on the meaning of ‘chloride-induced’ corrosion. They also indicate the way forward for the development of better analytical models for the prediction of expected corrosion.
- CHLORIDE-INDUCED CORROSION
The build-up of chlorides in the concrete matrix of reinforced concrete structures has long been correlated with the initiation and subsequent development of severe reinforcement corrosion. Although correlation does not prove any cause-effect relationship, the conventional wisdom has held for a long time that reinforcement corrosion will initiate when the surface chloride concentration on a reinforcing bar has reached a sufficiently high level, known as the ‘threshold concentration’ (e.g. Richardson, 2002; Hunkeler, 2005; Gjorv, 2009). Since the use of seawater as mixing water is no longer permitted, usually the principal source of chlorides is the external environment – typically marine but also from de-icing salts. Chlorides must thus diffuse (or otherwise travel) to the bars through the concrete cover. Together with the threshold notion of a critical concentration of chlorides initiating corrosion, this has led to the strong emphasis in modern practice for using concretes with low permeability and (ab)sorption characteristics and greater thickness of concrete cover. Also, there is much emphasis on the use of Fick’s second law to model chloride diffusion, with factors to allow for surface effects such as rainfall leaching, wet and dry cycling, and for the fact that the actual transport phenomenon is not purely diffusion (e.g. Hunkeler, 2005). These two ideas – chloride diffusion and the chloride threshold – underlie much of the present approaches to predicting the life of concrete structures (e.g. Richardson, 2002; Hunkeler, 2005; Gjorv, 2009; Angst, et al. 2009).
In practice, there are other effects that may render the conventional approach problematic. In seawater immersion and tidal environments, inward diffusion may be quite low due to the build-up of calcium and magnesium carbonates on the concrete surface that tend to act as diffusion barriers. While there has been extensive research over more than 20 years by many researchers focused on establishing the ‘chloride threshold’ at which corrosion initiates, the concept remains as elusive as ever, with very high variabilities between different environments, and high degrees of uncertainty (repeatability) even for nominally similar environments and conditions (Bentur et al. 1997, p 31; Angst, et al. 2009). The scenario does not change very much by invoking other criteria, such as the ratio of the concentration of chloride ions to the concentration of hydroxide ions in the concrete (i.e. (Cl–)/(OH–)) as initially proposed by Hausmann (1967).
The inability to relate chloride concentration closely with reinforcement corrosion shows that there is still imperfect understanding of the precise processes involved, despite many electrochemical (Bentur, et al. 1997) and laboratory investigations (Angst, et al. 2017). Increasingly it has become clear that the mechanisms involved in reinforcement corrosion are more complex than simply the direct action of chlorides attacking the steel of the reinforcement. As a result, the terminology ‘chloride-induced’ corrosion is now current. Following earlier work (Melchers & Li, 2006; 2009; Melchers 2010; 2015) herein it is considered that progress can be made in elucidating the mechanisms involved by using observations from actual concrete structures, particularly those that have shown, overall, excellent resistance to reinforcement corrosion, over extended periods of time.
- OBSERVATIONS FROM RC STRUCTURES
A useful overall summary of experiences with the long-term behaviour of reinforced concrete structures, including in chloride environments, has been given by Gjorv (2009). Also, a summary of many cases reported in the literature, extending back to the early 1900s, is available (Melchers & Li 2009). Both sources show that while there are many cases of reinforced concrete structures with poor durability and severe corrosion problems, there also are a considerable number of cases with excellent long-term performance. Both reviews suggest that much depends on achieving high quality, very low permeability concretes made with ‘good workmanship’. It also appears that concretes made with limestones and (non-reactive) dolomites have shown greater reinforcement durability than those made with igneous and similar aggregates (Melchers and Li, 2009).
Not everything attributed to chloride effects should be so attributed. Physical or chemical damage to the concrete matrix can be the instigator of subsequent ‘chloride-induced’ reinforcement corrosion. For example, road bridges without a bitumen wearing or riding course have been found to be subject to severe reinforcement corrosion, usually attributed to de-icing salts such as calcium and sodium chlorides applied during frost periods. However, closer observation showed that physical damage caused by motor vehicles and lorries to the bridge deck concrete cover was the prime cause of exposing the steel reinforcement to corrosion, rather than the inward diffusion of chlorides from de-icing salts (Beaton & Stratfull, 1963; Lukas, 1985; Volkswein & Dorner, 1986). Similarly, destruction of the concrete matrix protecting the steel may be caused by volume changes resulting from alkali-carbonate (ACR) and alkali-silica reactions (ASR). These causative mechanisms should be separated from corrosion attributed directly to chlorides (Jensen, 1996; Richardson 2002; Gjorv, 2009). It should be clear that once the concrete cover has been damaged the reinforcement is just steel exposed to the environment and will corrode as such steel normally would under those conditions, irrespective of any concrete properties. A further example is that of cracking transverse to the direction of reinforcement, noting that such cracking usually is the result of structural bending or shear. Conventionally, cracks in concrete up to about 0.3mm are considered acceptable, although this criterion was based mainly on testing of laboratory concrete specimens over relatively short-term exposure periods, including in simulated marine environments (Beeby, 1978). However, as shown below, for long-term exposures this criterion needs urgent revision.
While short-term testing and electrochemical testing are used in practice for estimating the expected life of a structure, such as for design and assessment purposes, any such testing must be validated against reality. It is in this area that problems tend to arise. Short-term accelerated tests such as using salt sprays, higher temperatures, impressed current on the reinforcement, etc., do not measure the same physical and (electro-) chemical features that drive long-term corrosion processes. Not only for reinforcement corrosion (Poursaee & Hansen 2009) but also more generally (Lee et al., 2010) the relationship between results so obtained and actual in-service behaviour remains tenuous. In brief, all accelerated test results require validation and this can be done only through comparison to actual field observations.
Since corrosion usually is a slow process, learning directly from field corrosion behaviour takes time. This is the case for experimental programs such as the Panama Canal Zone marine corrosion investigations extending over 16 years (Southwell & Alexander, 1970) and the NBS soil corrosion work (Romanoff, 1957) extending over a similar period. However, these did not deal with reinforcement corrosion and in any case are too short for much physical infrastructure, for which 50-100year lives are of interest. A complementary approach, used in the present investigations and also for assessing corrosion resistance for nuclear waste containers (Chitty et al., 2005) is what might be considered an ‘archaeological’ approach, in which behaviours of older structures and systems are examined, where necessary with reconstruction of operational and environmental scenarios and conditions.
Learning from actual operational experiences with real structures has the draw-backs that (1) usually there are few structures available for investigation, (2) they tend to be one-off so that investigation of causative parameters is difficult, and (3) typically they are not well-documented (or the documentation no longer exists or cannot be found). Nevertheless, several investigations along these lines have been described for reinforced concrete structures (e.g. Melchers et al. 2009; Angst et al. 2012). Fig. 1 shows an example for which there is a considerable amount of background information (Wood, 1948). This case and many others (Melchers, 2010, 2011, 2015) show some features in common, including:
1. Very high levels of chloride concentrations on reinforcing bars do not necessarily ‘cause’ other than very minor corrosion, and often no visual evidence of corrosion at all, for many years, often decades.
2. For high quality concretes, the onset of serious, damaging corrosion is considerably later in time than any measure of corrosion initiation.
3. The causative mechanism(s) for the commencement of serious reinforcement corrosion remain unclear but do not appear to be the same as those for corrosion initiation.
4. Very serious localised reinforcement corrosion without obvious external signs of corrosion such as rust staining and concrete cracking or spalling can and does occur but clear explanations for such corrosion remain outstanding.
Figure 1a. End and side view at low tide in 2009 of a Phoenix caisson similar to those used for the Normandy invasion, beached in Langstone Harbour, UK. The caisson was constructed on the adjacent coastline (Hayling Island) and broke its back (in 2 places) during launching in 1943. Note the high tide mark and the very modest evidence of reinforcement corrosion. The only aggregates available in this area are calcareous.
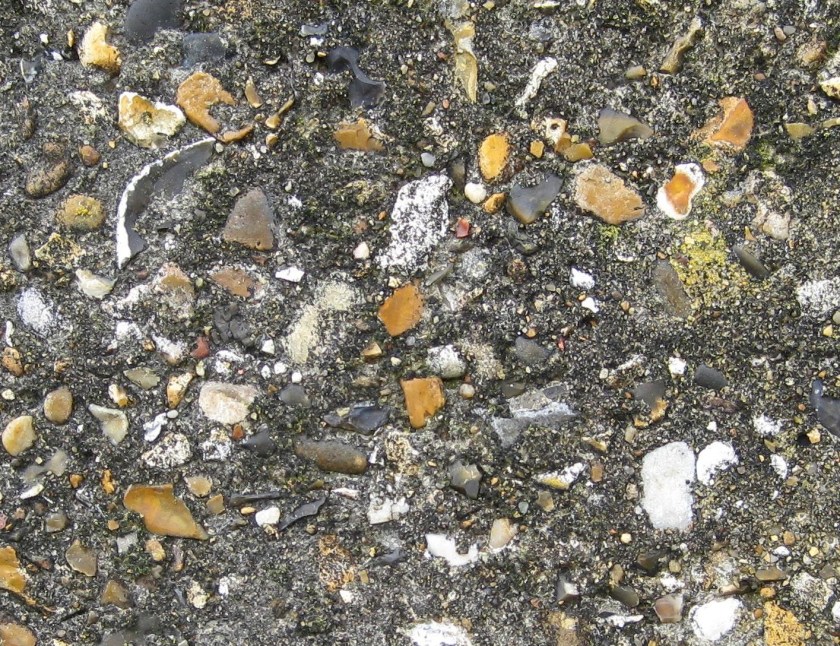
Figure 1b. Close-up view of calcareous aggregates and evidence of seashells in the concrete matrix. This suggests seawater was used as mixing water.
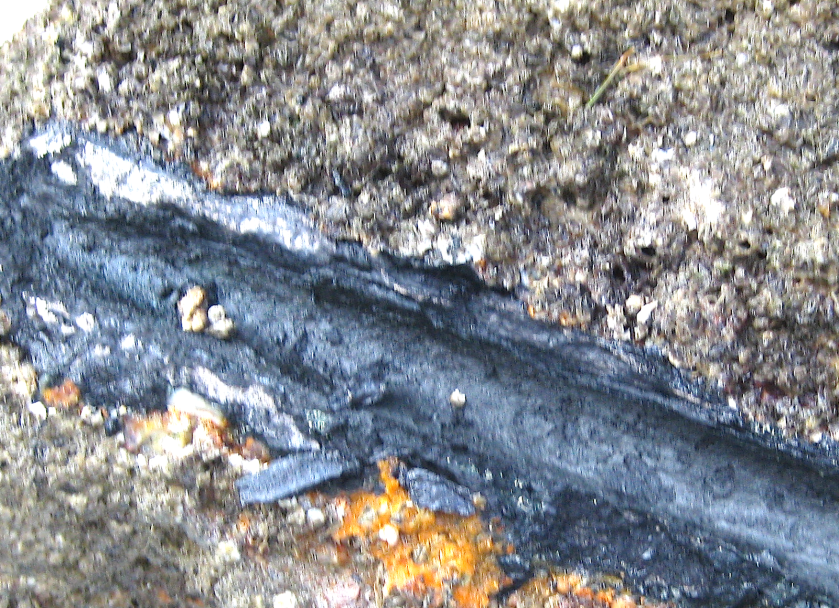
Figure 1c. Close-up view of a 16mm diam. reinforcing bar extracted from apparently sound concrete. There was no concrete cracking along the bar or normal red-brown rusts.
- MODELS FOR REINFORCEMENT CORROSION
- Corrosion Initiation and Active Corrosion
The conventional model for the commencement and development of reinforcement corrosion is that usually attributed to Tuutti (1982) but earlier proposed by Clear (1976) (Fig. 2a). It has negligible or no corrosion before the initiation time ti immediately after which corrosion becomes serious (Richardson 2002; Hunkeler 2005; Gjorv 2009). It has been proposed (Weyers et al., 1997; Bentur et al., 1997) that serious corrosion might occur at a time later than ti and that this delay is caused by the need for chlorides to diffuse from the external environment to the reinforcement, aided by minor cracking of the concrete, such as caused by beam bending (Francois & Arliguie, 1999).
On the basis of field studies (e.g. Melchers et al., 2009) and the examination of many reports, Melchers and Li (2006) proposed that the some limited amount of corrosion may commence at the initiation time ti but that serious long-term corrosion generally does not commence until some later time tact (Fig 2b). In this model, the period (0-ti) has essentially zero or negligible corrosion. This is followed, commencing at the initiation time ti, by some corrosion for a relatively short period of time, after which there is no or only a very modest increase in corrosion, until the commencement, at the activation time tact, of serious, damaging corrosion. Melchers and Li (2006) proposed that the corrosion process in the time period 0-ti differs from that causing the serious long-term corrosion. They also proposed that the active corrosion stage was the result of loss of concrete alkalis and in particular to the loss of Ca(OH)2 as accelerated by the presence of chlorides. This aspect is considered in more detail below in the light of recent research findings.
(a) (b)
Figure 2 (a) Classical model showing no corrosion (damage) until ti followed immediately by development of serious corrosion (damage), (b) modified model with separation between initiation at ti and start of active corrosion at tact (Melchers and Li, 2006).
Using the separation of ti and tact Melchers and Li (2009) reviewed and analysed some 300 individual reinforced concrete structures from details reported in the literature and in various reports. The analysis originally included cases of alkali-aggregate reactions (AAR) but these were later removed as not representative. The analysis reinforced the notion that a separation between ti and tact was very common in practice, at least for high quality reinforced concrete structures. The data from the analysis is summarised in Fig. 3. It shows the estimated values for ti and tact as functions of the estimated concrete chloride content for concretes made with two different types of aggregates. Despite the scatter in the data, it is clear that a considerable difference exists between ti and tact and that this applies for both types of aggregates. It is also clear that both times are greater for concretes made with (non-reactive) limestones and dolomites.
(a) | (b) |
Figure 3. Times to initiation (ti) or active corrosion (tact) as a function of concentration of chlorides estimated to be next to the reinforcement for (a) igneous and similar aggregates and (b) for carbonate type aggregates. Note the very considerable scatter in the data owing to disparate data sources. The typical range of acceptable chloride concentration threshold values is shown.
Recent, independent, support for the separation of ti and tact comes from observations of long-term laboratory exposures of pre-cracked beams (Yu et al. 2015). It was observed from periodic detailed observations that some corrosion had occurred in the period soon after first exposure but that subsequent observations showed this had ‘practically halted’ a short time later and remained so, before increasing again much later.
Apart from the clear difference between ti and tact, the most noticeable aspect of Fig. 3 is that the influence of chloride concentration on ti and tact is present for low concentrations of chlorides but is much less strong for high concentrations, again independent of type of aggregate used. The low influence of chloride content has been observed also for realistic reinforced concrete samples exposed for more than 10 years in a high humidity environment (Melchers & Chaves, 2017). These results contrast with many earlier laboratory test results that appeared to show chlorides as quite influential. However, the important difference is that most of these earlier observations were for samples exposed to accelerated test conditions or to test durations much shorter than 10 years (or both) and only seldom were real concretes used in the test programs. This suggests that those tests may not properly have represented conditions relevant to corrosion of steel bars inside actual concrete structures with realistic lifetimes.
In practice, the most critical aspect of reinforcement corrosion is the damage it does to the structure. As defined in Fig. 2b, this is active, damaging, corrosion associated with the time tact at which it commences. As now clear from Fig. 3 that irrespective of aggregate type and irrespective of chloride concentration, in general the commencement time tact is much later than the initiation time ti. This supports the notion that these two times are driven by different corrosion mechanisms. The possibilities for these are considered next.
- Some Theoretical Aspects
Before proceeding, it is helpful to revise briefly some basic concepts. For corrosion to occur, the thermodynamic requirements for the chemical reactions involved must be satisfied, that is, as expressed through Gibbs free energy or the equivalent Pourbaix diagram (Jones, 1996). Without an applied potential (such as often is applied in electrochemical tests, in pure water corrosion of ferrous iron can occur only for pH < about 9 (Pourbaix, 1970; Jones, 1996; Chitty, et al. 2005; Huet, et al. 2005). In waters containing chlorides, corrosion in the form of pitting can initiate at much higher pH, increasing with the chloride concentration (Pourbaix, 1970). These requirements govern whether it is possible for corrosion to occur. They are not informative about the rate of corrosion. However, for infrastructure applications it usually is the amount of corrosion loss, both general and localised, and the volume of damaging rusts produced that are the critical aspects. It follows immediately that initiation of corrosion as defined in Fig. 2b and given by time ti is of limited practical interest.
A freshly made concrete has a high pH, typically about 13.5 to 14, imparted by the minor constituent alkalis NaOH and KOH. These leach out relatively easily and then the principal alkali, calcium hydroxide, Ca(OH)2 tends to maintain a pH of about 12 and less as the concentration of Ca(OH)2 decreases. While such high pH is maintained at the steel interface corrosion cannot initiate – a drop in pH is required. Typically this is the case for ‘high-quality’ concretes – those made with adequate cement content (and type), and low permeability as usually reflected in higher concrete strengths and high density. Typically also, such concretes will have a high alkalinity (sometimes more easily visualised as the amount of ‘acid-buffering capacity’) and thus can absorb a large amount of ‘acid’ attack and still retain higher pH values. It follows that the rate at which pH can reduce with time is controlled by (a) the initial ‘alkalinity’ of the concrete, (b) the rate of leaching of alkalis from the concrete and possibly (c) the rate of ‘carbonation’. While pitting corrosion is possible for higher pH values in the enclosing environment, general (uniform) corrosion can occur only when the pH drops below about 9. Hence, for general corrosion a loss of alkalinity at the steel-concrete interface is required. In relation to Fig. 3b, it is noted that calcium carbonate (CaCO3) has very low solubility in water and produces a pH of around 10 – this may account for the larger values of ti and tact.
The above rather theoretical concepts are evident in careful examinations of practical cases. In one case (Melchers et al. 2009) the concretes were found to have retained their pH above 10 for more than 60 years, and only in very localized regions where the pH had fallen below 9, such as at hairline cracks in the concrete (presumably permitting entry of air, sea and rain water), was corrosion of reinforcement observed. Similar observations have been made for 80 year old reinforced concrete piles in tidal seawater (Melchers et al. 2017) and earlier also in other situations (e.g. Chitty 2005).
Turning now to active corrosion, the conditions under which it must occur inside good quality concretes can be characterized as ‘wet and stagnant’. Obviously, wetness is required for corrosion to occur but moisture must be present at the right location at the steel-concrete interface. Stagnant conditions have important implications for corrosion, as demonstrated in the classic work reported by Heyn & Bauer (1908). They observed little difference in corrosion loss for mild steel strips immersed in weak, circumneutral, but stagnant, solutions of many different salts, including NaCl. These observations were at first controversial but were explained eventually by Dora Brasher (1967). She argued that under stagnant exposure conditions the weak passive film that normally forms on mild steels, as first observed in the 1930s (cf. Evans, 1960), was able to remain in place and that under this condition the availability of oxygen governs the rate of corrosion. Carefully controlled laboratory exposure experiments by Mercer & Lumbard (1959) support this argument. They observed that a greater concentration of chlorides in water increased corrosion, but only in non-stagnant conditions. In stagnant or near-stagnant conditions chlorides had almost no influence on the amount of corrosion. One of the unfortunate aspects of many experimental laboratory testing programs is that stagnant conditions were seldom employed. Rather than using model concretes, these commonly used solutions, and often these were stirred, not stagnant, so as to speed up the corrosion process (Poursaee & Hansen, 2009).
- Time to Initiation
As noted above, much attention has been given in the corrosion literature to what has been termed the time to initiation (ti), with it being assumed, conventionally, that it corresponds to the commencement of serious reinforcement corrosion (i.e. in the notation of Fig. 2b it is assumed that tact = ti). However, if ti and tact are distinct, separate entities, based on the notion that they are governed by different mechanisms (Melchers & Li, 2006), as in Fig. 2b, the question arises what the mechanism is to cause ‘initiation’. This is being investigated in a long-term exposure experiment that commenced in 2004.
The experiment consists of exposing a large number of concrete specimens each 40 x 40 x 160 mm long, made to a variety of water/cement and aggregate/cement ratios all made with the same materials. Each specimen contains a single, longitudinally placed, 6 mm diameter smooth mild steel bar. Except for one test series as specifically noted below, all specimens were made using standard commercial (blended) Portland (GP-type) cement, sourced at the same time from one manufacturer. The specimens were all (and some continue to be) exposed continuously to a 25˚C high humidity (>95% RH) laboratory fog-room environment. This wet environment ensures carbonation can be discounted. Pacific Ocean seawater was used as mixing water for the majority of the samples with the remainder made with fresh (drinking) water. The exteriors of the specimens were observed to be water saturated whenever inspected in the fog room. One or two specimens from each sample set were withdrawn from exposure about every 12 months. These specimens were examined externally, and broken open to reveal the state of the steel reinforcement and also the condition of the interior concrete. Overall the patterns observed were consistent between years although some features increased with time. As noted earlier (Melchers & Chaves, 2017) the frequent sampling of one or two samples is slightly more informative than less frequent sampling of more samples at any one time.
Already after 2-3 years exposure, it was noted that many samples showed no corrosion and others showed only a limited amount of corrosion. Typically such corrosion was in the form of pitting or localized corrosion along the lower part of the reinforcing bar, away from the casting direction (Fig. 4a). This also was the side of the bars closest to the shaking table used for concrete compaction.
(a) | (b) |
Figure 4. (a) Typical early localized (pitting) corrosion along lower part of reinforcing bar but little or none elsewhere and (b) typical wet air-voids in concrete matrix adjacent to location of bars.
This pattern continued for the following years, with only moderate increases in corrosion observed. Typically, the concretes with the greatest apparent permeability and lower densities showed relatively more corrosion. After 10 years exposure the concretes with the highest aggregate cement ratios (i.e. lowest overall cement contents) and thus highest permeabilities showed moderate corrosion all around the reinforcing bars, but insufficient to cause longitudinal cracking along the bars. In contrast, even after 10 years the denser concretes (those with the lower aggregate/cement ratios) retained the pattern seen in Fig. 4a.
Particularly for the high density, low overall permeability concretes, examination of the interior concrete surfaces adjacent to the steel reinforcing bars showed, after the samples were broken open, the presence of multiple voids in the concrete surface, that is, within the thin Portlandite layer typically found around reinforcement bars. The voids contained air and were, like the surrounding concrete, wet, although not necessarily completely filled with water (Fig. 4b). The voids were found predominantly on one side of the bar, identified in all cases as along the bottom of the bars relative to the casting direction of the concrete in the steel moulds (Fig. 4a). Importantly, the concrete was vibrated on the laboratory shaking table with the moulds in the same orientation. Thus the bottom of the bars would be where any air-bubbles in the concretes would have been likely trapped. It was observed that the less dense concretes contained more air voids, including at the steel-concrete interface. Typically, the corrosion of the bars along their lower sides was in the form of pitting, often with multiple pits in close proximity, and considered, in the basis of the few observations that could be made both of the concrete and the immediate adjacent steel surface, to reflect the pattern of the voids. It was observed that the voids at the steel-concrete interface were more frequent and larger for the less dense concretes. For these concretes the pit density per unit area also was greater.
Multiple measurements made of concrete pH on the broken-open concretes, immediately next to the bars and away from them showed that even after 10 years exposure the pH values ranging from around 12 for the dense, low permeability concretes to around 10 for the less dense, apparently more porous or permeable concretes. Since the chloride concentrations in the pore-waters at the start of the experiment were similar to those of the seawater used for making the concrete (around 35,000 ppm), the only corrosion that could be considered to occur at that time (Pourbaix, 1970) was pitting corrosion. Indeed this is what was observed. Moreover, since the high chloride content existed from the start of the experiment, this would have been the case from the beginning and likely throughout the 10 years of experimental exposure, although there may have been some reduction in chloride concentration with time as a result of leaching. Nevertheless, the precise variation in pH (> 9) and the precise chloride content throughout that period are not critical – conditions suitable for pitting corrosion (only) would have prevailed at the beginning and most likely also throughout.
Voids in generally similar locations with respect to casting direction have been reported earlier for laboratory research projects on model concretes, although there was no mention whether vibration or other compaction techniques had been used (Horne et al., 2007; Bouteiller et al., 2012). In those experiments, local differences in pore water and concrete chloride content were observed for the region containing the voids. In addition, a number of other factors potentially important for corrosion in the concrete-steel interface region were identified but no conclusions drawn about their potential influence (Angst, et al., 2017). Also, no mechanism for corrosion initiation was proposed.
For real as distinct from model reinforced concretes there is a long history of observations of voids and separations at the concrete-steel interface. They are attributed to the degree of concrete compaction during construction (e.g. Nawy, 2008). However, voids and separations are not always observed, at least at a macro level. For example, two of the field studies mentioned above (Melchers et al.: 2009, 2017) showed no visible voids next to the reinforcement and, except at rare and very specific locations – see section 4.5 below – no sign of corrosion initiation, even after more than 60 and 80 years exposure to marine environments and very high concrete chloride concentrations. In both cases reinforcement corrosion was observed visually only where the local concrete pH was less than about 9. Both these structures were constructed before mechanical vibration equipment was widely available. This means that concrete compaction could have used hand rodding and hand tamping. It is readily verified that, if properly done, these hand techniques can deliver a concrete with negligible voids next to the reinforcement, even on the side away from the casting direction. A further factor is that, despite knowledge that limiting the water/cement ratio was important for strength, when these concretes were made, there were no specific limits on the amount of water that could be added to the mix, and emphasis in practice was on achieving workable mixes (Wood, 1948). This would have facilitated air bubbles leaving the steel-fluid concrete interface region during tamping, rodding or vibration, including on the underside of the bars.
Taking these observations together leads to the conclusion that corrosion initiation (at time ti) primarily is the result of the voids in the concrete next to reinforcing bars and that this is the result of imperfect concrete compaction. Specifically, it is proposed that the mechanism responsible for the initiation of reinforcement corrosion (i.e. that for ti as defined in Fig. 2b) is classical differential aeration (Evans, 1960; Jones, 1996) set up by cells of wet air voids immediately adjacent to the steel surface (Fig. 5). In this mechanism, the voids provide pockets of both air (and thus oxygen) and sufficient (usually oxygenated) water necessary to sustain the usual cathodic corrosion reaction within the void. Under the elevated chloride conditions present, the differential aeration will manifest as pitting corrosion, even under the high pH values of the concrete, with the pits forming at the edges of the wet air-voids (Fig. 5). Indeed, there are reports (Verbeek, 1975; Angst et al., 2017) of corrosion pits not aligning exactly with the centre of voids – and this can be interpreted as consistent with the scenario in Fig. 5.
Figure 5. Proposed model for localized corrosion (pitting) with wet air-voids as cathodic areas. |
For most concretes in marine environments, water in the form of pore water is likely to be available continuously inside the concrete matrix. Under these conditions the pitting corrosion process is likely to stop only once the oxygen in the air voids, or the oxygen dissolved in the pore water, is exhausted. Pitting corrosion may continue if permeability through the (wet) concrete permits some degree of oxygen diffusion from other voids in the concrete matrix or even from the external environment (Fig. 5). For wet concretes this is likely to be at a very low rate and thus any consequential corrosion also at a low rate. Obviously, the pitting effect will be very small for micro-sized voids and larger for macro-voids and explains why for very well-compacted concretes conventional aerated corrosion products usually cannot be observed. More generally, pitting may stop, perhaps only temporarily, if there is (a period of) insufficient pore water to sustain the corrosion reaction.
It has long been accepted that oxygen and water and in particular the humidity in the pores or voids are responsible for corrosion of reinforcement, and also that such pores (or voids) provide the necessary cathodic reaction (e.g. Andrade et al. 1990). However, the differential aeration mechanism shown in Fig. 5 and the fact that oxygen is limited mainly by that in the voids rather than by transport through the concrete cover has not been proposed previously.
Overall, the mechanism proposed above is consistent with various practical observations. For example, it has been observed that some corrosion after an initial period of exposure was followed by a quiescent period between ti and tact as shown in Fig. 2b (e.g. Francois & Arliguie, 1999; Yu, et al. 2015). The proposed mechanism also is consistent with the observation of rusts, such as ‘green rusts’, known to be formed under low oxygen conditions (Gilberg & Seeley, 1981), and often observed when the reinforcing bars are examined in the time period before tact (Melchers et al. 2009, 2017). These observations can be interpreted to reflect the gradual exhaustion of oxygen available, initially from the voids and eventually through oxygen diffusion. In this scenario also, the role of chlorides is simply to permit pitting corrosion to occur at a higher pH than without the presence of chlorides. In this sense chlorides induce the earlier occurrence of initiation. This is consistent with field observations (Fig. 3).
Finally in relation to the time to corrosion initiation, it is noted that for RC structures made with seawater, such as in the experiment described above, ti → 0 since the conditions for pitting corrosion under a high chloride environment were available from the start. For RC structures made without significant chloride levels but exposed to chloride environments, some time can be expected to elapse before these conditions are reached through chloride transportation through the concrete cover. It also can be expected that this time will be longer for lower external chloride exposure conditions. Indeed, this is in agreement with practical experience.
- Time to Active Corrosion
The time to active corrosion, tact, is of considerable practical importance. As noted earlier, in the past it has not always been separated from ‘initiation’. They may be closely linked in the case for poor quality, permeable concretes, but most field evidence for practical structures shows a very clear difference (Fig. 3). Estimates for tact often are based on observations of the time at which the concrete cover cracks or spalls as a result of the significant build-up of corrosion products, or when there are clear signs of rust staining. These actually are ex-post observations. They do not inform as to the mechanism(s) that might be involved in causing active reinforcement corrosion and thus the time tact. This is now explored.
As part of the experimental program outlined in section 4.3, one series of specimens (series C) was made with sulphate-resistant cement instead of commercial blended Portland (GP-type) cement used for all the other series. This had an unexpected benefit. Sulphate-resistant cement has the peculiar property that fresh cement or concrete made with it has a dark-grey-black colour. It is known to become lighter (within days) on exposure to the atmosphere as a result of oxidation of the iron and manganese sulphides that impart the dark colour (Hanson, 2015). However, for all concrete mixes made with this cement in the experimental program, a rim of lighter-coloured concrete was observed immediately the specimens were broken open (Fig. 6). Similar observations had been made already when specimens were broken open after 3 and subsequent years of exposure. At all times the light coloured rim or outer zone was wider for the more permeable concretes. Its width was also greater for longer exposure periods of corresponding concrete mixes. Specimens made with the commercial GP-type cement did not show the stark contrast such as in Fig. 6. However, a slight difference in colour between a darker inner core and a lighter outer zone could be observed for these also, similar to the patterns seen for the concretes made with sulphate resistant cement.
Figure 6. Specimen C4, made with seawater, showing the rim of light coloured concrete immediately after breaking the sample open after 10 years continuous fog-room exposure. The dark interior is typical of concrete made with sulphate resistant cement.
Analysis of the dark and of the light-coloured concretes such as those shown in Fig. 6 revealed interesting differences. When examined by scanning electron microscopy and energy dispersive spectroscopy (SEM/EDS) and x-ray diffraction (XRD) it was found that the light-coloured concrete was essentially devoid of Ca(OH)2 and also contained little or no C (and thus no calcium carbonate as would be caused by carbonation). In contrast, the dark coloured concrete was found to contain a high level of Ca(OH)2 (Melchers & Chaves, 2016). Similar observations were made for the light and dark concretes for other concrete specimens, irrespective of water/cement and aggregate/cement ratios.
The light-coloured concretes all showed relatively low (alkaline) pH readings, typically in the range 8.5 – 9.5, whereas the dark coloured concretes showed much higher pH readings (pH 10-12). The latter is consistent with the range of pH values for various concentrations of calcium hydroxide in solution.
When examined under the microscope the light-coloured concrete showed a much more open, and presumably more permeable, structure compared with the dark concrete from the inner zone, indicating material had been lost from the light coloured zone (Melchers & Chaves, 2016). It is postulated that because of this more open structure access of atmospheric oxygen became possible into the Ca(OH)2 depleted concrete, with the result that the iron and manganese sulphides of the sulphate-resistant cement oxidised and the dark-grey-black colour changed to the light colour observed. Thus the colour change is a consequential outcome of the outward leaching of hydrolysed calcium hydroxide. The overall results are summarized in Fig. 7.
Taken together, these observations show that, as proposed in 2006 (Melchers & Li, 2006), calcium hydroxide is lost progressively inwards from the outer parts of a concrete specimen, presumably by leaching after dissolution in water. Importantly, while the rate of dissolution of calcium hydroxide in pure water is very low (Sagues et al. 1997; Marinoni, et al. 2008), it is accelerated by the presence of NaCl in proportion to its concentration (Johnson & Grove, 1931). Important in this context is that more permeable concretes have a greater internal surface area available for the dissolution process. The patterns seen in Fig. 7 are consistent for all the concrete mixes made with sulphate resistant cement – the only difference being that the width of the lighter-coloured concrete was greater for concretes with higher permeability (as estimated using rebound (Schmidt) hammer surface hardness readings) (Melchers & Chaves, 2016).
Internal view | Internal view |
Internal pH spot-readings | Internal pH spot-readings |
Concrete mix C2: w/c = 0.65 a/c = 2:1 Dense, low permeability concrete | Concrete mix C7: w/c = 0.65 a/c = 6:1 A concrete of high permeability |
Dark grey inner zone, light grey outer zone | Only light grey concrete |
Negligible corrosion and superficial anoxic rusts | Corroded reinforcement bar |
EDS: Ca, Si, and C, Al and Mg. Also O. | EDS: similar, but low counts for C |
XRD: High Ca(OH)2 | XRD: No Ca(OH)2 detected |
(a) | (b) |
Figure 7. Appearance of interior concretes and condition of the reinforcing bars after 10 years exposure in the laboratory fog-room. There are clear differences in the interior pH values and in the composition of the concretes, with high calcium hydroxide present in the dark concrete and no calcium hydroxide in the light coloured concrete.
To estimate the effect of chlorides on the above mechanism, two other series (B and K) of experiments was conducted in parallel to those for series C described above. These were treated as described above – in addition the depth (d) of loss of Ca(OH)2 (i.e. depth of the light-coloured concrete) was measured for each specimen. The results are shown in Fig. 8a as a function of rebound hammer surface hardness readings and in Fig. 8b as a function of water/cement (w/c) and aggregate/cement ratios (a/c).
Fig. 8b shows that there is little effect for a/c ratios 2:1 and 4:1 for any of the three concrete series. It also shows that the concretes with the greater a/c ratio of 6:1 have a much greater loss of calcium hydroxide as measured by d. As noted above, this is likely because of the greater openness (porosity) of concretes with such high a/c ratios permitting greater areas available for dissolution. The mixes (series C) made with sulphate resistant cement show, in all cases, much greater d than the corresponding series B. This is consistent with the sulphate resistant cements producing lower strength, and thus more permeable, concretes. For the similar a/c ratios of 4:1 and 6:1 the freshwater (series K) show d values roughly half of those for the seawater concretes (series B). This is consistent with chlorides (in the B series) increasing the rate of calcium hydroxide dissolution.
(a) | (b) |
Figure 8. Depth (d) of loss of calcium hydroxide as a function (a) of rebound hammer reading as a (inverse) surrogate for concrete permeability and (b) of water/cement and aggregate/cement ratios.
Although the scatter in each set of data points is high, the data do show trends when fitted with a best-fit plotting routine. The concretes made with sulphate resistant cement (series C) show much greater depth of calcium hydroxide loss than the concretes made with GP-type cement (series B). Both Figures show that the depth of calcium hydroxide loss is about 100% more for the concretes (of given w/c and a/c ratios, or similar surface hardness values) made with seawater (series B) compared to those made with fresh water (series K).
An important practical observation in these results is the effect of concrete permeability (Fig. 8a). Loss of calcium hydroxide is much higher and thus at a higher rate for permeable concretes than it is for dense and impermeable concretes. This is consistent with practical observations that concrete structures provided with good quality and adequate depth of cover and that are made from low permeability concretes survive much longer without obvious reinforcement corrosion (Gjorv, 2009). Again, this was observed also for the cases mentioned in Section 3, except where the concrete had cracked. In this context it should be noted that the results shown in Fig. 8 are for concretes that were uncracked. Cracking can be expected to have an influence on the rate of loss of alkalis.
- The Influence of Concrete Cracking
Under stress, RC elements tend to develop cracks perpendicular to the line of reinforcement, although the pattern may be more complex if high levels of concrete shear stress are involved. These cracks have long been considered as possibly contributing to a loss of protection as normally provided by the concrete cover (cf. Francois & Arliguie 1999). Longitudinal cracks on the other hand usually are the result of corrosion rather than a direct cause of reinforcement corrosion.
Early studies on the possible effect of concrete cracking on reinforcement corrosion came to the conclusion that cracks were of little importance and that autogenous healing often would reduce any long-term effect, a view supported by observations of high concrete pH values adjacent to cracks and, in some cases, the use of freshwater. Also, for cracks that penetrated to the reinforcement the severity of any resulting corrosion appeared to be directly proportional to crack width (Beeby, 1978; Bentur et al., 1997, p. 50). Others considered the presence of a crack to be more important than its width (Mohammed et al., 2001). Importantly, most of these conclusions were based on relatively short term testing and on observations on structures constructed with limestone or similar aggregates. As noted above, these aggregates tend to impart greater alkalinity (or acid-neutralising buffering capacity) to the concrete. This will aid autogenous healing.
Recently large-scale laboratory testing has shown that irrespective of their width, cracks transverse to the reinforcement direction permit the commencement of corrosion at the crack base. Such corrosion may then extend along the damaged steel-concrete interface (Francois et al., 2012). Also, observations for actual reinforced concrete structures have provided strong evidence that cracking transverse to reinforcing bars, even hairline cracking, only barely observable, can cause severe and very localised corrosion of the bars, particularly in longer term exposure conditions (Fig. 9) (Melchers & Li, 2009; Melchers et al., 2017). This might be expected since such cracks would tend to expose more of the concrete matrix to the possibility of alkali dissolution. As proposed above, it is the rate of alkali dissolution that is the critical corrosion rate controlling process. In the extreme, widespread cracking would expose more concrete matrix to the possibility of alkali dissolution and thus reduce the duration over which the concrete can provide adequate, alkaline, and thus
acid-neutralisation buffering protection. In the present context this is in relation to the effect of chlorides but a similar effect would apply to carbonation. In both cases, this should have a direct effect on the likely effective lifetime of reinforcement in concrete structures.
Figure 9. Example of very severe localised corrosion of 6mm diam. reinforcement in concrete exposed for more than 60 years to a marine environment and for which there were no obvious external signs of reinforcement corrosion. |
- MODEL FOR CHLORIDE INDUCED CORROSION
The above observations and the model shown in Fig. 2b lead directly how the expected lifetime tL of a RC structure subject to ‘chloride-induced’ corrosion should be modelled:
tL > tact (= ti + tpass ) (1)
where ti is the time to corrosion initiation as before and tpass is the time period after initiation and before active corrosion commences. As shown in Fig. 2b, the expected lifetime tL will include some period during which corrosion is already active. Estimation of the period of time during which such active corrosion can be tolerated without impairment of structural performance or structural serviceability is the subject of considerable recent research, particularly in structural engineering. Here that period is considered a bonus beyond the time tact at the commencement of serious corrosion.
Despite the model for the initiation mechanism proposed above, quantifying the time to initiation remains an issue for research investigation, now with parameters such as compaction and size of voids to be considered. The time period tpass represents a rather similar difficulty, since it has not been main-stream in research activity and there have been no concerted efforts, empirical or otherwise, to investigate it. At the present time it would appear that the best way forward is to focus on estimating tact directly. Again, currently there is only limited published research focussed on estimating tact directly but a first estimate can be made using information such as that used in obtaining Fig. 3 and also information such as presented in Fig. 8. Further, a conservative estimate of tact can be obtained by assuming the chlorides are present from the very beginning, thereby obviating the need to estimate the time for chlorides to migrate into the concrete. In this respect the results in Fig. 8 can be considered conservative since chlorides were present from the start.
For example, consider a (uncracked) concrete with a high water cement ratio of 0.6 and an aggregate cement ratio of 4:1. If made with fresh water Fig. 8 suggests that the depth of loss of calcium hydroxide would be d = 1.1mm in 10 years or 0.11/y. If the concrete was made with seawater then d = 3.2 mm over 10 years or 0.32/y. This means that a concrete structure with a cover of 50mm would commence with active corrosion after 450 and 160 years for fresh water and for seawater respectively, assuming, of course, uncracked concrete. While these estimates might appear to be very high, the estimate for concrete with high concentrations of chlorides is not completely unrealistic. It can be compared to the case of the Hornibrook Bridge piles, exposed to Pacific Ocean immersion, tidal and splash zones. These showed, after 80 years, almost no loss of calcium hydroxide from the concrete matrix and pH readings around 12, despite very high chloride concentrations, around ten times the normally accepted threshold (Melchers et al. 2017). However, as noted in section 4.4 above, where there was concrete cracking through to the reinforcing bars very serious corrosion had occurred. This was also the case for the 60 year-old RC structure with the quite localised but very severe corrosion shown in Fig. 9. As suggested in section 4.4, the critical aspect to life prediction for RC structures now appears to be the effect of (transverse) cracking of the concrete matrix to a depth significant enough to accelerate the loss of calcium hydroxide or other alkalis.
- DISCUSSION
From a practical perspective, the most important parameter to arise from the present work is tact. It describes when serious corrosion can be expected to commence, irrespective of any previous, short-term initiation as indicted by the parameter ti. In most practical structures, it is the case that once serious corrosion has commenced the lifetime of the structure has been seriously compromised. Certainly simulations can be carried out to ascertain the extra life (to tL) possible after tact has been reached, but the aim in any design or rehabilitation exercise should be to extend the time horizon for tact as long as can be achieved, economically.
The second practical outcome from the present work is the clear indication that cracking of the concrete, particularly transverse cracking through to or close to the reinforcement, such as might result from high bending stresses, can have a very detrimental effect on the expected life of reinforcement against corrosion. An immediate implication from the present work is that, apart from any role such cracks may have for inward transport of chlorides and/or oxygen, they provide pathways for outwards leaching of alkalis and thus for the lowering of pH adjacent to reinforcing bars, thereby eventually permitting the commencement of active corrosion, initially localised at the crack opening. If such cracking is extensive, for example as usually the case in beams subject to bending or from temperature changes, the effect is similar to overall loss of permeability of the concrete cover. Earlier research results that permitted limited concrete crack sizes in design specifications appear to have ignored the effect of crack depth and must now be considered inadequate. As noted, that research was based on short-term testing and did not allow development of the mechanisms exposed by the present longer-term experimental work, seen in the various field observations and also seen in other recent experimental work (cf. Francois et al. 2012). It follows that design rules for cracking need to be revised, particularly for marine exposure conditions.
The third aspect to arise from the present work is that it reinforces the crucial role of concrete alkalinity. The importance of this has long been recognised as a key factor in maintaining passivity against corrosion of steel reinforcement. The recent experimental results for chloride induced corrosion reinforce this role since alkalinity dissolution is now seen to be critical in the development of conditions that permit commencement of active, serious corrosion of the reinforcement, including in chloride environments. Since high alkalinity conventionally is associated with high cement contents, the immediate inference is that longer durability can be achieved with higher cement content. However, opposing this are the increasing environmental and economic pressures to reduce cement contents in concretes. In this context, the results shown in Fig. 3b are important as they suggest that there are other ways of boosting the acid-neutralisation capacity of concretes, namely with (a relatively high proportion of) low alkalinity aggregates such as limestone and non-reactive dolomites. It is clear that when these were used as aggregates they increased the time tact to active corrosion. This observation is consistent with (anecdotal) experience, for example, in those parts of Europe (Lukas, 1985) and in Florida (Lau et al., 2007) where the predominant aggregates are calcareous. It also is consistent with difference in RC durability between different locations within the US with longer durability corresponding to those for which the predominant sources of concrete aggregates are calcareous (Melchers & Li, 2009). For these various cases, the potentially lower strength of limestones (but not of dolomites and, for example, marble) has not been noted as a significant (negative) factor. These considerations also suggest that there may be other ways to increase the alkalinity of concretes, such as the addition of other types of alkalis to the mix. This is an obvious area for research. Another area for research is the balance between the greater use of cement to increase the effective life of a structure subject to durability issues, and the increased serviceable life thus obtained. It may be that the negative environmental impact of a higher use of cement initially is outweighed by a lower overall use over the life of a RC structure through not having to renew it in toto or repair it.
An important aspect of the present work is that the models underlying Fig. 2b and Eqn. 1 largely are derived from observation, directly or indirectly, of the behaviour of actual RC structures or sufficiently realistic surrogates. The approach used relies only indirectly on observations from usually rather artificial laboratory studies such as those using surrogate solutions for pore-waters rather than using concretes. There also is little reliance in the present work on the results from electrochemical tests since these, too, are conducted under rather artificial and often under accelerated conditions. Mostly these techniques have limitations (Lee et al. 2010; Poursaee & Hansen, 2009), not always made explicit, that could have serious implications for translation of the experimental results to realistic structures. Rather than attempting to untangle the issues involved with these various techniques, the present work has focussed on observations and interpretations from actual structures, despite some well-known difficulties of interpretation and data support, particularly for older cases.
The propositions in the present work have have indicated a number of areas for further research additional to those mentioned above. The estimation of tact (and tpass) still represents a significant research challenge. The variables likely to be involved have been mentioned in the exposition above, but their interaction and their direct effect on tact remain to be further explored, including:
1. alkalinity of the concrete as determined by the cement content and added alkalis,
2. internal surface area available for alkali dissolution (related to concrete matrix density and permeability),
3. rate of (chloride-driven) alkali dissolution (a function of the chloride concentration (Johnston & Grove 1931),
4. effect of concrete cracking on concrete permeability and on serious (perhaps only localised) reinforcement corrosion.
In addition, in practice it can be expected that there will be a degree of interaction between chloride inward diffusion resulting in the slow increase in chloride concentration (in 1) and the effect of that concentration on the rate of alkali dissolution in (3). This aspect, too, remains for further research.
Finally, the overall mechanisms described herein differ from the conventional wisdom in some important ways. They give a role to chlorides that differs significantly from the conventional wisdom, and one that differentiates between initiation of reinforcement corrosion and its eventual serious, active, commencement. Overall, the mechanisms are consistent with fundamentals in corrosion science and, importantly, are consistent with practical experience and observations for high quality reinforced concrete structures. The present results also bring a degree of unity between carbonation-induced and chloride-induced corrosion. In both cases it is the loss of protective alkalinity that permits eventual, active corrosion.
- CONCLUSION
Recent research has shown that the primary role of chlorides in so-called ‘chloride-induced’ corrosion of reinforcement lies in accelerating the solubility of the alkaline calcium hydroxide in the concrete matrix, including around the reinforcing bars and thereby eventually allowing depassivation of the steel reinforcement. Typically, this takes a long period of time and is influenced, strongly, by concrete permeability and concrete alkalinity, such as provided by cement or by alkaline aggregates. On the other hand, the mechanism for corrosion initiation is primarily the result of poor compaction around the reinforcing bars allowing localised differential aeration corrosion cells. The separation of corrosion initiation from the commencement of active reinforcement corrosion, the dissolution of alkalinity and the role of major concrete cracking all throw new light on the way the time to serious reinforcement corrosion under chloride conditions should be modelled. A framework for such modelling is outlined, as are the research challenges.
- ACKNOWLEDGMENTS
The author acknowledges the financial support of the Australian Research Council for some of the work reported herein. The support of the Civil Engineering laboratories at the University of Newcastle, in particular Ian Jeanes and Goran Simundic, the suggestion of (the late) Dr Dick van der Molen to try sulphate-reducing cement, the earlier research support of Dr Torill Pape and more recently Dr Igor Chaves in sample analyses and the support from Central Scientific Services at the University of Newcastle are all acknowledge with much gratitude. In addition, the helpful comments and suggestions from the reviewers are appreciated.
- REFERENCES
Andrade, C., Alonso, C. & Garcia, A.M. (1990), Oxygen availability in the corrosion of reinforcements, Advances in Cement Research, 3(11) 127-132.
Angst, U.M., Elsener, B., Jamali, A. & Adey, B. (2012), Concrete cover cracking owing to reinforcement corrosion – theoretical considerations and practical experience, Materials and Corrosion, 63(12) 1069-1077.
Angst, U.M., Elsener, B., Larsen, C.K. & Vennesland, O. (2009), Critical chloride content in reinforced concrete – A review, Cement and Concrete Research 39, 1122-1138.
Angst, U.M., Vennesland, O., Larsen, C.K. & Elsener, B. (2017), Chloride induced reinforcement corrosion: results from a laboratory study within the Norwegian COIN project, Proc. 3rd Intl. Congress on Durability of Concrete, Adelaide, 22-25 Oct.
Angst U. M. and 15 others (2017), The steel-concrete interface, Materials and Structures, 50 (143) (24 pp.)
Beaton, J.L. & Stratfull, R.F. (1963), Environmental influence on corrosion of reinforcing in concrete bridge substructures, Highway Research Record, 14, 60-78.
Beeby, A.W. (1978), Corrosion of reinforcing steel in concrete and its relation to cracking, The Structural Engineer, 56A(3) 77-80.
Bentur, A., Diamond, S. & Berke, N. (1997), Steel Corrosion in Concrete: Fundamental and Civil Engineering Practice, E&FN Spon, London.
Boqi, C., Dinghai, H., Hengquan, G. & Yinghao, Z. (1983), Ten-Year field exposure tests on the endurance of reinforced concrete in harbor works, Cement and Concrete Research, 13, 603-610.
Bouteiller, V., Cremona, C., Baroghel-Bouny, V. & Maloula, A. (2012), Corrosion initiation of reinforced concretes based on Portland or GGBS cements: Chloride contents and electrochemical characteristics versus time, Cement and Concrete Research, 42, 1456-1467.
Brasher, Dora M. (1967), Stability of the oxide film on metals in relation to inhibition of corrosion. I. Mild steel in the presence of aggressive ions, British Corrosion Journal. 2, 95-103.
Broomfield, J.P. (1999), Corrosion of steel in concrete, E. & F. Spon, London.
Burnside, O.H. & Pomerening, D.J. (1984), Survey of experience using reinforced concrete in floating marine structures, Report SSC-321, Ships Structures Committee, US Coast Guard Headquarters, Washington DC.
Chitty, W.-J., Dillmann, P., L’Hostis V. and Lombard, C. (2005), Long-term corrosion resistance of metallic reinforcements in concrete – a study of corrosion mechanisms based on archaeological artefacts, Corrosion Science 47, 1555-1581.
Clear, K.C. (1976), Time-to-corrosion for reinforcing steel in concrete slabs. V. 3: Performance after 830 daily salt applications, FHWA-RD-76-70, Federal Highway Administration, Washington, D.C., Apr., 64 pp.
Dewar, J.D. (1963) The workability and compressive strength of concrete made with seawater, Tech Rep, TRA/374, C&CA, London.
Escalante, E. & Ito, S. (1990), Measuring the rate of corrosion of steel in concrete, (In) NS Berke, V Chaker & D Whiting (Eds) Corrosion Rates of Steel in Concrete, ASTM STP 1065, Am. Soc. Testing Materials, Philadelphia, pp. 86-102.
Evans, U.R. (1960), The corrosion and oxidation of metals: scientific principles and practical applications, London, E. Arnold.
Francois, R. & Arliguie, G. (1999), Effect of microcracking and cracking on the development of corrosion in reinforced concrete members, Magazine of Concrete Research, 51(2) 143-150.
Francois, R. Khan, I., Vu, N.A., Mercado, H. & Castel, A. (2012), Study of the impact of localized cracks on the corrosion mechanism, European J. of Environmental and Civil Engineering, 16 (3-4) 392-401.
Gilberg, M. R. & Seeley, N. J. (1981), The identity of compounds containing chloride ions in marine iron corrosion products: A critical review. Studies in Conservation, 26(2) 50–56.
Gjorv, O.E. (1971,) Long-time durability of concrete in seawater, ACI J. 68(1) 60-67.
Gjorv, O.E. (1994), Steel corrosion in concrete structures exposed to Norwegian marine environment, Concrete International, 16(4) 35-39.
Gjorv, O.E. (2009), Durability design of concrete structures in severe environments, London, Taylor & Francis.
Hanson (2015) Sulphate-resisting cement: Technical data sheet, Version 3.3, November 2015, Hanson Heidelberg Cement, Ketton, UK.
Hausmann, D.A. (1967), Steel corrosion in concrete, Materials Protection, 6(11) 19-23.
Heyn, E. and Bauer, O. (1908), Ueber den Angriff des Eisens durch Wasser und wässerige Losungen, Stahl und Eisen, 28(44) 1564-1573.
Horne, A.T., Richardson, I.G. & Brydson, R.M.D. (2007), Quantitative analysis of the microstructure of interfaces in steel reinforced concrete, Cement and Concrete Research, 37, 1613-1623.
Huet, B., L’Hostis, V., Miserique, F. and Idrissi, H. (2005), Electrochemical behavior of mild steel in concrete: influence of pH and the carbonate content of the pore solution, Electrochimica Acta, 51(1) 172-180.
Hunkeler, F. (2005), Corrosion in reinforced concrete: processes and mechanisms, (In) Corrosion in reinforced concrete structures, (Ed) H Bohni, Woodhead Publishing Limited, Cambridge, 1-45.
Jensen, V. (1996), Present experience with aggregate testing in Norway, (In) Proceeding of the 10th International Conference on Alkali-Aggregate Reaction in Concrete, Melbourne, Australia, 133-142.
Johnston, J. and Grove, C. (1931), The solubility of calcium hydroxide in aqueous salt solutions. Journal of the American Chemical Society, 53 (11) 3976–3991.
Jones, D.A. (1996), Principles and Prevention of Corrosion, Second Edition, Upper Saddle River, NJ, Prentice-Hall.
Lau, K., Sagues, A.A., Yao, L. and Powers, R.G. (2007), Corrosion performance of concrete cylinder piles, Corrosion, 63(4) 366-378.
Lee, J.S., Ray, R.I. and Little, B.J. (2010), The influence of experimental conditions on the outcome of laboratory investigations using natural coastal seawaters, Corrosion 66(1) 105001-1 – 6.
Lewis, D.A. (1962) Some Aspects of the Corrosion of Steel in Concrete, Proceeding of the First International Congress on Metallic Corrosion, London, 1962, pp. 547-555.
Lewis, D.A. and Copenhagen, W.J. (1959), The corrosion of reinforcing steel in concrete in marine atmospheres, Corrosion, 15(7) 382t-388t.
Lukas, W. (1985), Relationship between chloride content in concrete and corrosion in untensioned reinforcement on Austrian bridges and concrete road surfacings, Betonwerk und Fertigteil-Technik, 51(11) 730-734.
Marinoni, N., Pavese, A., Voltolini, M. and Merline, M. (2008), Long-term leaching test in concretes: An X-ray powder diffraction study, Cement & Concrete Composites, 30, 700-705.
Mather, B. (1964), The effects of sea water on concrete, Misc Paper 6-690, US Army Engineering Waterways Experimental Station, Vicksburg, MI4.
Melchers, R.E. (1999), Structural Reliability Analysis and Prediction (2nd Edn.) John Wiley, Chichester.
Melchers R.E. (2004), Pitting corrosion of mild steel in marine immersion environment – 1: maximum pit depth, Corrosion, 60(9): 824-836.
Melchers, R.E. (2010), Carbonates, carbonation and the durability of reinforced concrete marine structures, Australian J Structural Engineering 10(3): 215-226.
Melchers, R.E. (2011), Observations about the corrosion of reinforcement in marine environments, Proc. XII DBMC, Int. Conf. on Durability of Building Materials and Components, Porto, Portugal, April 12-15, CDRom, paper 6.59.
Melchers, R.E. (2015), Field experience and the long-term durability of reinforced concrete structures, Proc. Second Intl. Conf. on Performance-based and Life-cycle Structural Engineering (PLSE 2015), Brisbane, 9-12 Dec., University of Queensland, Brisbane.
Melchers, R.E. & Chaves, I.A. (2016), Long-term durability of reinforced concrete structures in marine environments, Proc. Eurocor2016, Montpellier, 11-15 Sept.
Melchers, R.E. & Chaves, I.A. (2017), A comparative study of chlorides and longer-term reinforcement corrosion, Materials and Corrosion, in press.
Melchers, R.E. & Li, C.Q. (2006), Phenomenological modelling of corrosion loss of steel reinforcement in marine environments, ACI Materials Journal, 103(1): 25-32.
Melchers, R.E. & Li, C.Q. (2009), Reinforcement corrosion initiation and activation times in concrete structures exposed to severe marine environments, Cement and Concrete Research 39, 1068-1076.
Melchers, R.E., Li, C.Q. & Davison, M.A. (2009), Observations and analysis of a 63-year old reinforced concrete promenade railing exposed to the North Sea, Magazine of Concrete Research 61(4) 233-243.
Melchers, R.E., Pape, T.M., Chaves, I.A. & Heywood, R. (2017), Long-term durability of reinforced concrete piles from the Hornibrook Highway bridge, Australian Journal of Structural Engineering, in press.
Mercer, A.D. & Lumbard, E.A. (1995), Corrosion of mild steel in water, British Corrosion J., 30 (1) 43-55.
Mohammed, T.U., Otsuki, N., Hisada, M. & Shibata, T. (2001) Effect of crack width and bar type on corrosion of steel in concrete, J. Materials in Civil Engineering (ASCE), 13(3) 194-201.
Narver, D.L. (1954), Good concrete made with coral and seawater, Civil Engineering, 24(11) 49-52.
Nawy, E.G. (2008), Concrete Construction Engineering Handbook, CRC Press, Boca Raton, pp. 30-57.
Ozaki S. & Suguata, N. (1998) Long-term durability of reinforced concrete submerged in the sea, (In) Concrete under severe conditions 2: environment and loading, Vol. 1, Proc. Second Intl. Conf. on Concrete under severe conditions, CONSEC’98, Tromso, Norway, June 21-24, (Ed.) O.E. Gjorv, K. Sakai and N. Banthia, E & FN Spon, London, 448-457.
Parrott, L.J. (1987), A review of carbonation in reinforced concrete, Building Research Establishment, Department of the Environment, UK.
Pourbaix, M. (1970), Significance of protection potential in pitting and intergranular corrosion, Corrosion, 26(10) 431-438.
Poursaee, A. & Hansen, C.M. (2009), Potential pitfalls in assessing chloride-induced corrosion of steel in concrete, Cement and Concrete Research 39, 391-400.
Richardson, M.G. (2002), Fundamentals of durable reinforced concrete, SponPress. London.
Romanoff, M. (1957), Underground Corrosion, National Bureau of Standards Circular 579, US Government Printing Office (Publishers), Washington DC.
Sagues, A.A., Moreno, E.I. and Andrade, C. (1997), Evolution of pH during in-situ leaching in small concrete cavities, Cement and Concrete Research, 27 (11) 1747-1759.
Shalon, R. & Raphael, M. (1959), Influence of seawater on corrosion of reinforcement, J. ACI, 30(12) 1251-1268.
Sharland S.M. & Tasker P.W. (1988) A mathematical model of crevice and pitting corrosion – I. The physical model, Corrosion Sci. 28(6), 603-620.
Southwell, C.R. & Alexander, A.L. (1970), Corrosion of metals in tropical waters – Structural ferrous metals, Materials Protection 9(1) 14-23.
Tuutti, K. (1982), Corrosion of steel in concrete, Swedish Cement and Concrete Research Institute, Stockholm, Research Report No. 4. (see also (1984) Service life of structures with regard to corrosion of embedded steel, (In) Performance of concrete in marine environment, ACI SP-65, American Concrete Institute, Detroit, 223-236.)
Verbeek, G.J. (1975), Mechanisms of corrosion of steel in concrete, Publication SP-49, American Concrete Institute, Farringham, MI, 21-38.
Volkswein, A. & Dorner, H. (1986), Untersuchungen zur Chloridkorrosion der Bewehrung von Autobahn-Brucken aus Stahl-oder Spannbeton, Forschung Strassenbau und Strassenverkehrstechnik, Heft 460, Bundesminister fur Verkehr, Abteilung Strassenbau, Bonn-Bad Godesberg, Germany.
Wakeman, C.M., Dockweiler, E.V., Stover, H.E. & Whiteneck, L.L. (1958), Use of concrete in marine environments, Proc. ACI 54(4) 841-856.
Wells, T. & Melchers, R.E. (2015), Modelling concrete deterioration in sewers using theory and field observations, Cement and Concrete Research, 77, 82-96.
Weyers, R.E. (1997), Corrosion service life model concrete structures, (In) Repair and rehabilitation of reinforced concrete structures: The State of the Art, (Ed) WF Silva-Araya, OT De Rincon and LP O’Neill, ASCE, Reston, VA, 105-119.
Wig, R.J. & Ferguson, L.R. (1917), Reinforced concrete in sea water fails from corroded steel, Engineering News-Record, 79, 689-693.
Wood, C.R.J. (1948), “Phoenix” (In) The Civil Engineer at War, A symposium of papers on war-time engineering problems, Vol 2 – Docks and Harbours, London: The Institution of Civil Engineers, 336-368.
Yu, Linwen, Francois, R., Vu Hiep Dang & Gagne R. (2015), Development of chloride-induced corrosion in pre-cracked RC beams under sustained loading: Effect of load-induced cracks, concrete cover, and exposure conditions, Cement and Concrete Research, 67, 246-258.
- AUTHOR DETAILS
![]() Robert E. Melchers is Professor of Civil Engineering at The University of Newcastle, Australia. He holds a BE and MEngSc from Monash University and a PhD from the University of Cambridge, UK. He is a Fellow of the Australian Academy of Technological Sciences and Engineering and an Honorary Fellow of The Institution of Engineers Australia. His most recent awards are the 2009 ACA Corrosion Medal, the 2012 Jin S Chung Award (International Society of Offshore and Polar Engineers) and the 2013 John Connell Gold Medal (The Institution of Engineers, Australia). He was the Institution of Engineers, Australia Structural College Eminent Speaker for 2014. |