Case study on thermal insulating coatings on oil and gas assets for reducing CUI Risk.
By Daniel Lillas Fabric Maintenance Coordinator, ACA, NACE, Coating inspector, ICORR PFP & Insulation inspector
Introduction
The use of personal protection insulation is designed to provide a physical barrier against personnel being able to contact hot or cold surfaces in an effort to protect personnel from injury.
Traditionally the process systems selected for PP insulation are operating at temperatures that could cause hot or cold burns, and have been insulated with a physical insulation system either traditional jacketed insulation or mesh type guarding.
Some historical data has shown that the traditional insulation methods result in serious CUI threats and failures, mainly due to the service temperatures being within a favorable CUI range, and moisture being able to enter the insulation through some point throughout the systems lifecycle.
Common Flaws.
With some traditional insulation used for personnel protection systems operating within the +50°c to +100°c once a moisture path has been created and insulation becomes wet, there is the potential in for cyclic convection to occur, by which the moisture evaporates at the contact point of the substrate and only to re-condense upon contact with the cooler inner surface of the weather jacket.
In most cases this goes unnoticed as the pipe or equipment is covered from view by the outer jacket, some traditional inspection methods may identify telltale signs of CUI, but often at a late stage.
Other methods such as perforated mesh guarding have been a way to combat this issue by allowing free flow of any moisture and therefore eliminating the chance of moisture cycling, however this also has flaws, as traditionally the mesh is fabricated from stainless steel and when coupled with carbon steel components sets up a galvanic corrosion cell, to combat this the mesh is sometimes fixed to the equipment using a barrier of some type, and often a woven fiberglass tape. However, once the tape has been subjected to moisture over a period, the tape can absorb the moisture and allow a long time of wetness to occur at that localized spot, thus setting up a CUI location at the contact point, this is however could be considered the lesser of two evils, given that the ability to visually inspect the CUI location is present.
Similarly, when the stainless-steel mesh is in direct contact with carbon steel components at terminations of guarding, the corrosion point can exist either by galvanic coupling or abrasion.
Alternative thinking.
The introduction of new technology using thermal insulating coating instead of traditional insulation as an alternative by applying a liquid coating to the substrate and providing a thermal barrier through composite ceramic and silica based insulating coating.
Some coatings are water based acrylics, comprised of air filled ceramic and silica beads held in suspension by an acrylic binder.
Figure 1-example of insulating coating technology
Case Study.
After experiencing several coating failures and corrosion issues from both hot insulation and personnel protection insulation systems on an offshore facility a coating trial was implemented using a thermal insulating coating system.
The environmental corrosion conditions on the facility had experienced extreme atmospheric and CUI rates as high as 800µm/yr (corrosion rates determined through material loss from original thickness suffered over the length of time the facility was 1st put into service).
Two locations were selected for the trial.
- 600mm diameter hydrocarbon line
- Re-boiler heat exchanger nozzles
TRIAL 1 Hydrocarbon line temperature | TRIAL 2 Re-Boiler exchanger temperature | ||
Bottom | 67°c | Area 1 | 92°c |
middle | 72°c | Area 2 | 92°c |
top | 88°c |
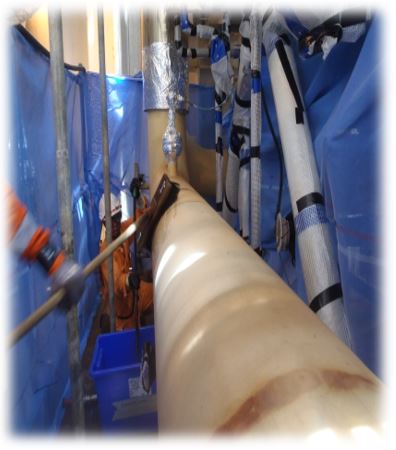
The coating was applied to the two locations over a washed surface of previously coated surfaces and cleaned with a vinegar solution as per manufacturer’s directions, each of the locations had the insulating coating spray applied to various thicknesses and once cured, surface temperatures were recorded to show the reduction in substrate temperature. The purpose of personal protection insulation in general is to reduce temperatures to an acceptable level, which is generally <50°c and there are many occupational health and safety standards that individually deal with protection of personal of exposure to hazards including hot / cold surfaces, and such there is no direct rule that suits all industries, but is generally determined by individual companies.
TRIAL 1 piping system-Atmospheric conditions during application average 76.5% relative humidity and 31.5°c air temperature.
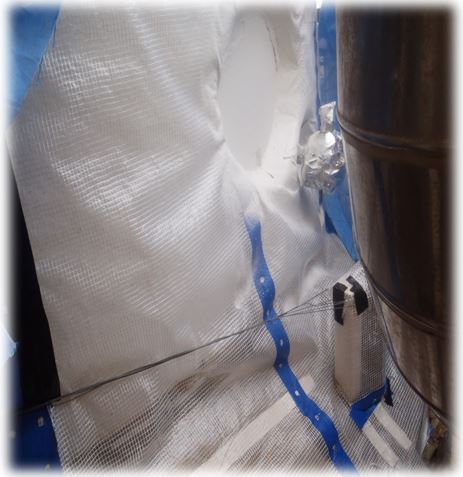
TRIAL 2 Exchanger shell plate- Atmospheric conditions during application average 73.5% relative humidity and 31°c air temperature.
Results.
Trial 1 location-piping system 3 separate areas were coated and an average of 18.6°c temperature drop was recorded
AREA 1 | |
Thickness(DFT) | 2000µm-2500µm |
Uncoated Temperature | 67°c |
Coated Temperature | 51°c |
AREA 2 | |
Thickness(DFT) | 2000µm-3000µm |
Uncoated Temperature | 72°c |
Coated Temperature | 58°c |
AREA 3 | |
Thickness(DFT) | 2000µm-2500µm |
Uncoated Temperature | 88°c |
Coated Temperature | 62°c |
Trial 2 location exchanger vessel shell above nozzles, 2 locations were coated with the insulating coating, and the results were again successful as trial 1 with a reduction of surface temperature on average 31.5°c. Area 2 was applied with additional film thickness for the trial to highlight the potential reduction of temperature with the dry film thickness increments. The manufacturer has guidelines of coating thicknesses for specific conditions, the trial used both manufacturers recommendations and experimental thicknesses to provide evidence of coatings performance potentials.
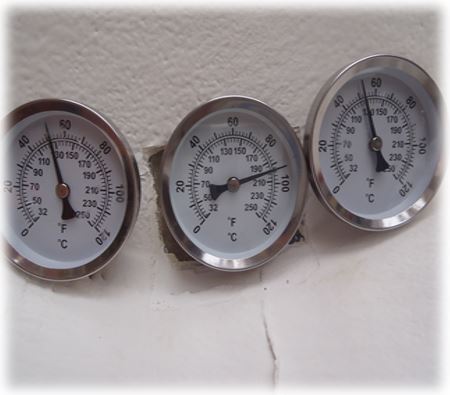
AREA 1 | |
Thickness(DFT) | 2200µm-2500µm |
Uncoated Temperature | 92°c |
Coated Temperature | 68°c |
AREA 2 | |
Thickness(DFT) | 3000µm-3200µm |
Uncoated Temperature | 92°c |
Coated Temperature | 53°c |
Discussion and Conclusion
The trial of insulating coatings on both areas proved successful in reducing the surface temperatures to be within the companies acceptable limits to be considered for thermal insulation removal for personnel protection. The considerations for use of thermal insulating coatings versus traditional insulation systems could become a viable alternative as shown in the trial, with consideration to thermal performance in process systems the coating in many cases could be used in varied applications within processing industries. The reduction in temperature at the surface without traditional insulation provides an alternative in combatting CUI threats from moisture being trapped within the insulation systems and reactions of coatings with leachable contaminants.
In addition, the use of external coatings of this nature allow for visual inspection of any early failure within the coating system without the need to remove any external jacketing, thus reducing the risk of “hit and miss” type of inspection regimes.
The coating used in the trial is suitable for both ferrous and non-ferrous substrates, which provides further potential for protection against conditions such as: Chloride induced stress corrosion cracking of stainless steels with the advantage of allowing free drainage of any moisture, and removal of external influences from within insulation materials producing unfavorable PH levels.
The coating after some time was observed to suffer some micro cracking and may not be a suitable anti-corrosion coating when used by itself in aggressive environments, the coating if used in conjunction with a suitable topcoat could provide excellent results, a topcoat with reasonable flexibility such as acrylic would be generally suitable to allow movement of the underlying insulating coating. In addition, an underlying anti-corrosion primer could also be considered to improve corrosion resistance in aggressive environments.
The coatings were applied directly to hot substrates, as a trial, the properties of the coating exhibited some discolouration on the hotter surfaces. The coating has great potential as an alternative to traditional insulation in selected applications and with further consideration to being coupled with other coatings as a full coating system.
Other substrates could also be considered such as Glass Reinforced Plastic(GRP) and other composites, such applications as water services. In addition, there could be a possibility of formulating the coating within the resins of epoxies, plastics when manufacturing composite piping much the same way pigments or additives are used.
Acknowledgements:
C. Kinsella- report and material for case history
D. Lake, N. Sequera – review and support material.