In the courtyard of a ruined mosque at the Qutub Minar complex not far from Delhi’s Indira Gandhi International Airport in northern India, stands a pillar of iron that has remained rust-free since it was fabricated in ~400 A.D. The 6-ton pillar was originally forged and erected in central India during the Gupta period, but moved to its present site about seven centuries ago. Although the climate in Delhi is not particularly corrosive—at ~20 µm/y for mild steel (ISO category C2)—this cannot explain the rust-free condition of the pillar. As a result of its remarkable state, the pillar has fascinated historians and archaeologists, as well as those of us with scientific and technical interests, for many years.
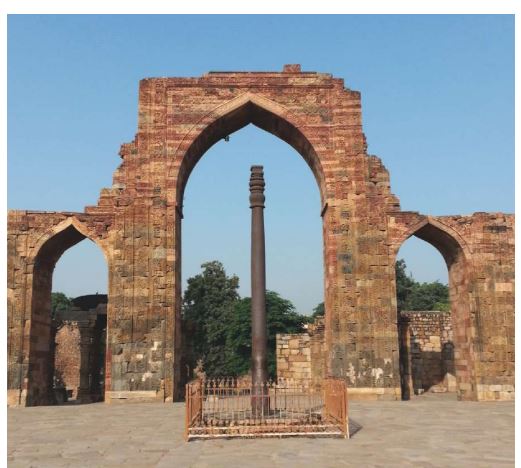
The solid iron pillar is ~7-m high and ~400-mm in diameter at the base. The lower part is rough and pitted where it was once below ground, but the rest of the cylindrical column is smooth and tapers to a decorative bell at the top. An inscription commemorates the victory of King Chandra over his enemies in the fourth century A.D. There is also damage that is believed to be caused by a cannon shot. The massive pillar was not built in one piece, but rather by hammering together several pieces of hot wrought iron in a process known as forge welding. The composition is not homogeneous; the carbon content varies widely, as is the case for other ancient wrought iron. The average composition of the Delhi Pillar, compared to a typical modern steel of similar carbon content, is shown in Table 1.
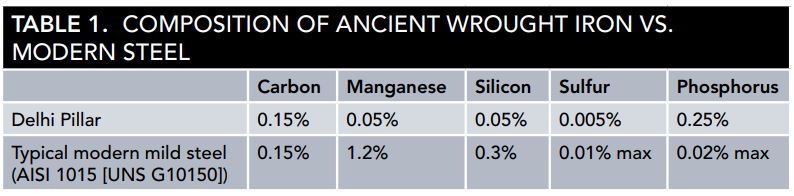
Apart from the phosphorus level that is over 10 times that of a modern steel, the level of impurities in the pillar is generally low, which is typical of ancient wrought iron. A high phosphorus iron ore was clearly used, and this element contaminated the product. As a result, a very thin dark grey protective layer of crystalline iron hydrogen phosphate has formed on the surface of the pillar, which is the reason for its resistance to corrosion.
Surely then we just need to increase the phosphorus content of modern steel to prevent it from rusting? Unfortunately, this amount of phosphorus has a detrimental effect on the steel’s mechanical properties. While the Delhi pillar iron has quite a high yield strength typical of modern structural steel, the phosphorus has greatly reduced its ductility as measured by elongation.
The impact toughness would be similarly reduced. A steel with such a high phosphorus content would be far too brittle and suffer from a problem that is known as “cold shortness” (“short” is an old term meaning brittle, as in short bread). It was recognized many years ago that limits on phosphorus in steel were needed. In fact, the first standard issued by ASTM in 1901, ASTM A1 for railway rails, included a limit on the phosphorus content. A high phosphorus content doesn’t matter for a pillar that just stands there, but it is totally unacceptable for anything subjected to stresses, such as a bridge, building, rail, or any mechanical device. The mechanical properties of ancient TABLE 2. MECHANICAL PROPERTIES OF ANCIENT WROUGHT IRON VS. MODERN STEEL Yield Strength Tensile Strength Elongation Delhi Pillar 324 MPa 330 MPa 5% Typical 350 MPa (50 ksi) steel 345 MPa 450 MPa 25% wrought iron, compared to a typical modern steel of similar carbon content, are shown in Table 2.
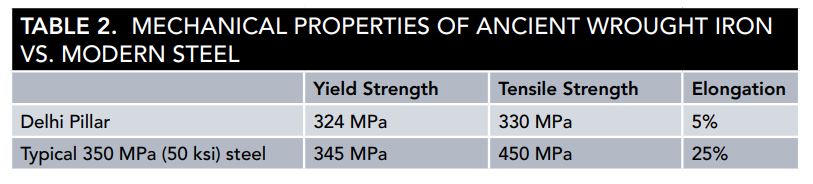
Although the ancient Indian blacksmiths (accidentally) achieved rust-free iron 1,600 years ago, it was, unfortunately, at the expense of useful mechanical properties. In the November 2018 issue of MP, we will see how clever manipulation of the chemical composition can produce truly rust-free steel with acceptable mechanical properties, which has been used to produce one of the modern wonders of architecture.