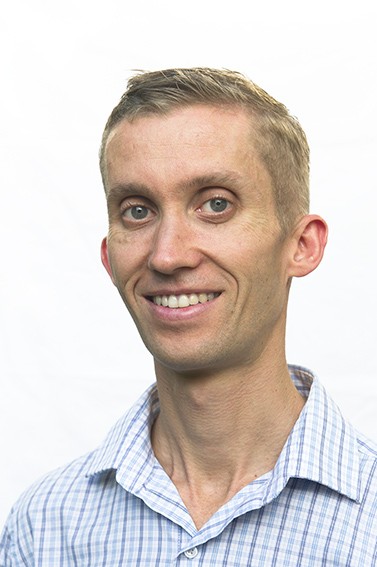
Simon Krismer
Bureau Veritas
Principal Consultant
Role
Bureau Veritas is a world-leading provider of conformity assessment solutions to the consumer product services market. Bureau Veritas provides a large range of services, including certification, marine classification, HSE, coal and mineral analysis, and asset integrity services.
The group that I work for is Asset Integrity and Reliability Services, which is a group dedicated to helping industrial clients manage their critical assets, equipment and infrastructure. Bureau Veritas predominantly provides Non-Destructive Testing and Condition Monitoring services, but we also have a Materials Science and Engineering group that carries out metallurgical consulting and failure analysis services, which I am part of.
I am a specialist in mechanical equipment failure analysis, covering all manner of machinery and plant types. Root Cause Analysis (RCA) is my expertise.
My predominant work is for the coal mining industry, but I also consult to manufacturing plants, OEM’s, fabricators and workshops. Examples of how we add value for our clients may include; improving reliability and productivity, assisting with warranty claims, material specifications, repair specifications, reverse engineering, etc.
As a principal consultant, my role is to provide high-level technical consultancy to our clients, and also to provide technical support and mentorship for my colleagues.
Favourite Corrosion Project
It is so hard to pick a favourite! I have worked on just about every conceivable type of corrosion issue. From exotic things like liquid metal embrittlement of Monel 400 by Mercury and high temperature issues such as oxidation, metal dusting and carburization; MIC related failures of stainless steels, carbon steels and copper; unusual corrosion causes such as ozone attack of 316L and “ants nest” corrosion of copper pipes; corrosion induced mechanical failures such as fatigue cracking caused by corrosion pitting or fretting, or bearing failure due to water ingress causing staining; to plain and simple rusting of steel structures.
But to be honest, the cases I really enjoy are the less obvious ones, which require deep thought and logical analysis to determine the root cause. One which comes to mind is sulfide stress cracking (SSC) of a stainless steel flexible hose on a coal seam gas wellhead.
The initial challenge was to correctly identify the failure mode, but the next challenge was to determine the source of the sulfide. It turned out that hydrogen sulfide was being generated by the action of SRB in the “hard” water containing gypsum (calcium sulfate).
Issues Facing the Industry
It is apparent that different industries have very different levels of awareness of corrosion management and prevention. In particular, the insidious corrosion issues that can cause plant failures are generally not identified in most asset management plans, or unfortunately not even considered during the design stage.
Many of the failures that we see are very easily preventable – typically for the cost of some form of suitable corrosion protection system.
It is vital that engineers improve their knowledge and awareness of corrosion and its potential effects when developing specifications and asset management plans.
ACA Membership
I have found that the ACA provides a unique forum where a diverse range of people from all types of business and all walks of life can unite.
Rather than a just being a collection of peers from the same industry/qualification there are amazing opportunities to network and learn from the broader “corrosion” community.
This was clearly demonstrated at our recent conference in Sydney. As a consultant working towards solving problems for a range of industries, it is fantastic to be a member of the ACA.