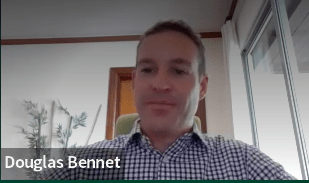
Over 100 registrants from 17 countries participated in our first Technical Group event of 2023, a webinar about “Latest Insights into Microbial Influenced Corrosion (MIC) Monitoring Techniques” held on the 14th February . It indicates the importance of this topic to corrosion practitioners.
The Oil & Gas Technical Group committee members were delighted with the presentation of two experts from overseas, Douglas Bennett (Intertek, Malaysia) and Danika Nicoletti (LuminUltra, Canada). Did you miss it? Check out the event review and get in touch with the Oil and Gas Technical Group here. The webinar was moderated by Arthur Kokolekos and Dr Margarita Vargas, longstanding members of the Oil & Gas Technical Group and both very familiar with MIC and the problems it can cause in the oil and gas industry.
Douglas Bennett started by explaining that MIC, once an exotic topic is now thought to be responsible for 10-50% of overall corrosion.
Given that the global cost of corrosion has been estimated to be $2.5 trillion by AMPP (formerly NACE) MIC is a huge cost anywhere in the world. For example the MIC cost in Malaysia alone is estimated at $900m.
Douglas explained that whilst MIC is usually associated with sulfate reducing bacteria (SRBs) they are not the only active species and bugs capable of participating in MIC exist everywhere.
MIC activity is strongly affected by presence of biofilm. The microbes are very social and exist in mixed communities.
He then went on to explain the different diagnostic tests for MIC bacteria. Traditional serial dilution and culturing is still used but can take up to 28 days to get results for SRBs. Quick tests such as ATP and immunology (antibody) type test kits give a fast result but at the expense of accuracy and specificity. On the other hand DNA tests including PCR analysis (most accurate), DGGE – denatured gel analysis and FISH – fluorescent in situ hybridization are much more accurate than culturing and rapid tests, but need specific equipment and trained technicians. The most comprehensive results are produced from NGS – next generation sequencing but again this requires trained operators to carry out.
But tests don’t measure corrosion – they detect microorganisms and indicate risk or threat eg high bug numbers. Most important is that personnel need to be trained to take a microbial sample in the field and that it may be necessary to use multiple testing techniques. There are a lot of stakeholders in the field who want quick answers. But these results then need to be backed up with more detailed analysis and interpretation.
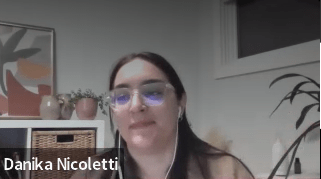
Our second speaker, Danika Nicoletti explained how traditional methods of microbial monitoring such as MPNs, bug bottles, etc favour fast growing organisms, not always relevant to MIC bacteria. Also whilst there are some very powerful, but time-consuming methods available the trend nowadays is moving towards quicker, more accurate testing.
She mentioned some interesting work on how qPCR can be used to target biomarkers relevant to MIC mechanisms. Eg outer membrane cytochrome on desulfovibrio ferrophilus that can specifically take up electrons from steel. Also, corrosive methanogens which can catalyse steel corrosion.
ExxonMobil correlated severe corrosion rates with micH gene and NGS enables ability to identify metabolism of microorganism eg sulfate reducers.
Danika emphasized the importance of a holistic monitoring program combining both rapid and detailed tests. For example:
ATP – total biomass monitoring maybe daily
qPCR – monthly monitor for specific microorganisms
NGS – maybe yearly to ensure no problem species arise.
Danika also touched on the case of accelerated low water corrosion, an important form of MIC in marine environments where anaerobic conditions may exist under biofilm colonies so it is possible to have MIC induced by anaerobic microorganisms even seemingly aerobic conditions.
Finally, Danika suggested some areas where the industry could implement improvements in MIC practice. She again emphasized the importance of proper sampling – the quality of data depends directly on sampling method.
In conclusion, she made the case for sharing of knowledge between different companies and groups who work on MIC in the field. There are many different organisms involved in MIC and they cooperate. Work on eg biomarker trends would greatly benefit from collaboration between different groups.
Membership of the ACA Oil & Gas Technical Group is open to corrosion engineers and scientists with an interest or involvement in the oil & gas, petroleum or chemical industries. Enquiries about the Group’s activities should be directed to the secretary: Philip.fleming@harrison.com.au