The Australian Transport Safety Bureau have released their report on flight QFA94 that resulted in a mid air engine failure and as a result turned back to LAX in May last year
After hearing a loud bang multiple cabin crew called the flight deck to advise that the aircraft was vibrating in an unusual way. Some of crew had seen sparks and flames from the engine. This was useful to the flight crew as no automated fire alarms had been triggered in the cockpit and no fire detected.
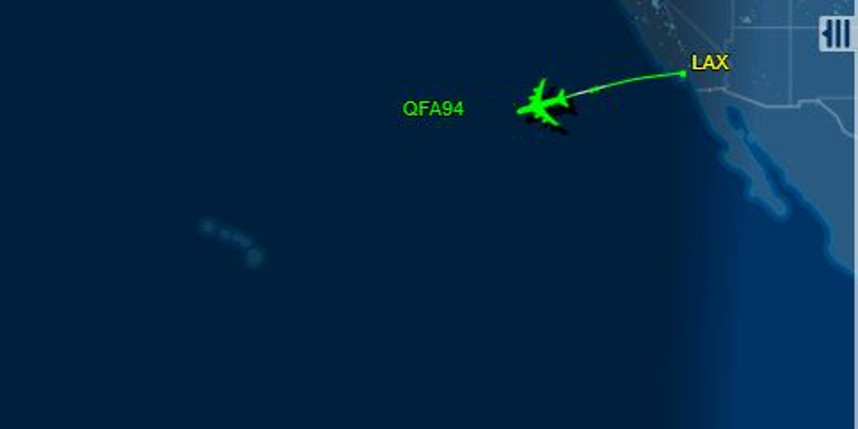
Engine shutdown
As the plane had not yet reached the halfway mark to Honolulu the Captain decided to return to LAX.
This heavily loaded ,Melbourne bound, plane jettisoned fuel over the Pacific to allow a landing at LAX. After a normal approach the Captain used the entire length of the runway to stop the plane in an effort to reduce load on the brakes and the resulting sparks.
Despite mid air reports of fire none could be detected by the LAX firefighter team and the Captain was allowed to taxi to the gate and not have to evacuate the plane.
The ATSB Investigation
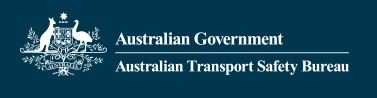
Initial engineering inspection of the No. 4 engine following the incident found damage to the low‑pressure turbine blades. There was no visible indication of fire and the event was contained, such that there was no breach of the engine casing. There was minor damage to the right flap and flap fairing from debris exiting the rear of the engine.
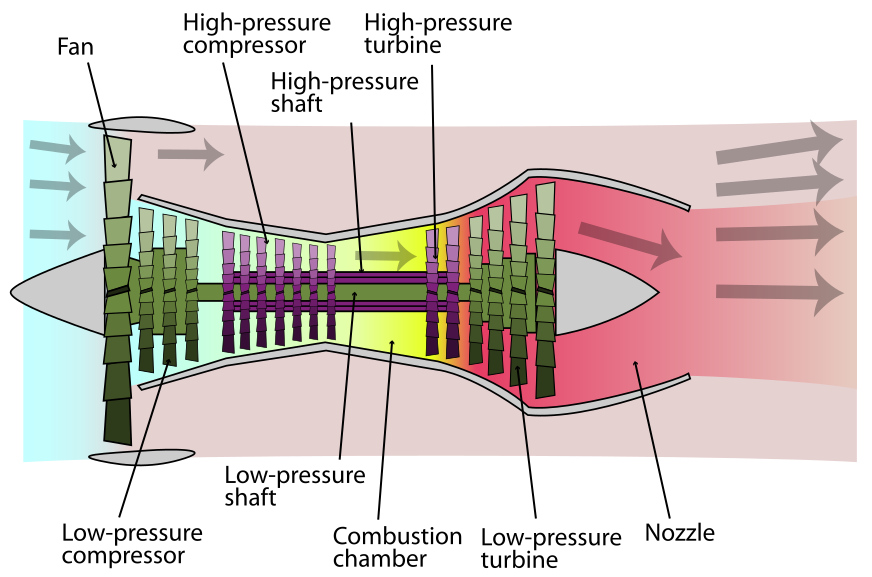
A later ATSB teardown of the engine found internally-corroded low-pressure turbine stage 2 (LPT2) blades. The corrosion led to fatigue cracking and subsequent release of blade shroud debris, resulting in significant downstream engine damage.
The corrosion resulted from chemical residue in the hollow turbine blades from cleaning operations
Rolls-Royce, the manufacturer of the aircraft’s Trent 900 engine, conducted an investigation into the engine failure that caused the shutdown.
In addition to the stage 2 turbines already identified as corroded by the ATSB . Rolls Royce found that the Stage 5 low pressure turbine blades had been exposed to the same cleaning process and the same corrosion issue identified.
Since the incident, an audit by Rolls Royce found 12 other engines potentially affected by the cleaning process and as a result a thorough audit of cleaning operations has been implemented
Rolls Royce also revised its blade cleaning procedures and instructions.
Blade overhaul cleaning operation instructions were revised, with additional detail to incorporate best practice with respect to removal of process solutions and chemical residues. This included modifying the orientation and support of the blades during the cleaning process and pressurised water flushing of aerofoil cavities after cleaning to ensure removal of residual cleaning fluids.
You can read the the full ATSB report here
The Corrosion Mechanism
This is the corrosion fatigue mechanism – when corrosion due to residues of cleaning chemicals can initiate metal fatigue this causes cracking and/or failure to occur in metal, such as a turbine fan blade.
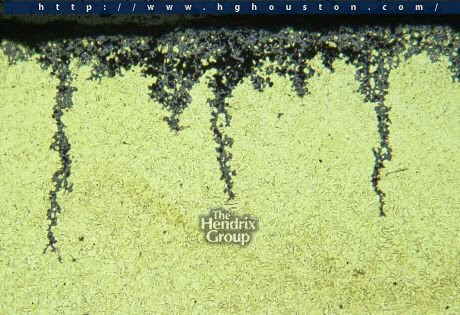
Les Boulton who initially alerted us this story has provided some more information on short notice. Thanks Les!