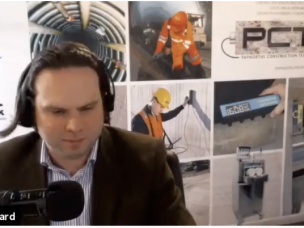
Cathodic Protection of Concrete Structures Q&A Webinar
The ACA NSW Branch hosted a unique Q&A webinar session on cathodic protection of steel-reinforced concrete structures, featuring six industry-leading guest speakers. Our guest panel discuss impressed current, hybrid, and sacrificial CP systems as well as some related topics submitted by the audience.
25th August 2020